Achieving reliable results in Commissioning, Qualification, and Validation (CQV) is essential for maintaining product quality, ensuring patient safety, and complying with regulatory standards in pharmaceutical and medical device manufacturing. However, the CQV process can be complex and requires careful planning, execution, and continuous monitoring. Ensuring reliability in CQV results can prevent costly delays, regulatory penalties, and quality issues.
This blog will provide you with 10 practical tips that can enhance the reliability of your CQV outcomes, helping you maintain seamless operations and regulatory compliance.
1. Develop a Comprehensive Validation Master Plan
A robust CQV Master Plan (CQVMP) is the foundation of any successful CQV process. This plan should serve as the roadmap for all activities, ensuring that all objectives are clearly outlined and stakeholders are aligned. The CQVMP should cover essential aspects like timelines, the scope of work, personnel roles, and a clear definition of responsibilities.
It’s crucial to prioritize critical systems and equipment and address any potential challenges early in the planning stage. Additionally, ensure that the CQVMP aligns with industry standards and regulatory requirements, particularly for products that may require ongoing validation efforts. A comprehensive and well-thought-out plan can streamline the entire process, reduce unnecessary delays, and ensure the overall reliability of your CQV results.
2. Conduct Thorough Risk Assessments
Risk assessments are a key component of the CQV process and must be done before proceeding with validation activities. These assessments help identify potential risks in equipment, processes, and systems, allowing you to focus your resources on high-priority areas. For instance, processes involving sterile environments, high-risk drugs, or devices should be flagged as critical and validated with utmost caution.
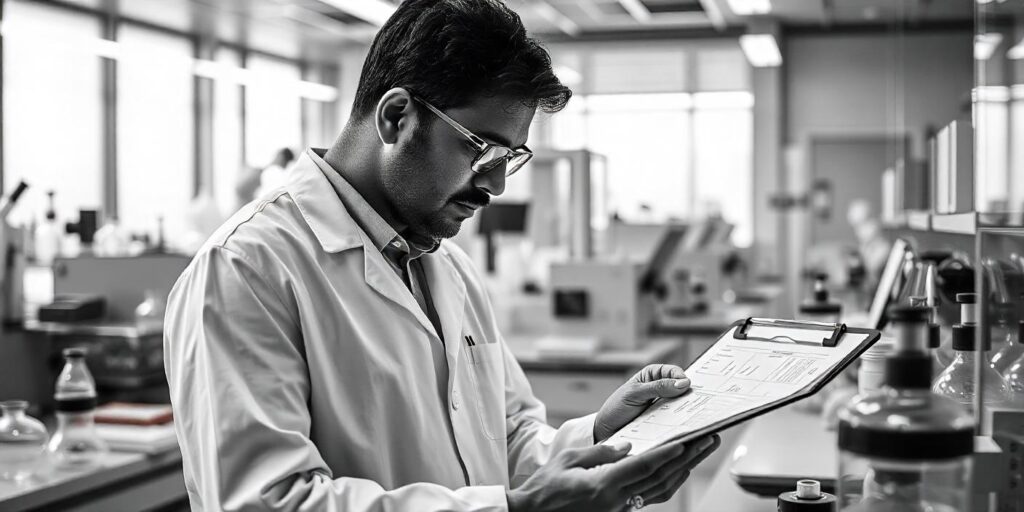
Using methods like Failure Mode and Effects Analysis (FMEA) helps predict areas of failure and mitigate risks before they affect the overall CQV outcome. By prioritizing high-risk activities and addressing them first, you can ensure that the most critical aspects of your CQV process are validated properly. Ultimately, this contributes to more reliable CQV results and reduces the potential for product failure or regulatory non-compliance.
3. Ensure Adequate Training for Teams
The quality and reliability of your CQV results depend significantly on the people executing the validation protocols. Ensuring that all personnel involved are adequately trained and well-versed in both regulatory requirements and operational procedures is essential for success. Training should include an understanding of the entire CQV lifecycle, from commissioning through qualification to final validation.
In addition to initial training, ongoing education and regular assessments should be part of your team’s professional development to stay updated on any regulatory changes or new technologies that could impact the validation process. Well-trained teams can identify and address issues early on, making the entire process more efficient and less prone to errors.
Read More: 7 Tips to Train Your Team Better on Compliance
4. Focus on Robust Documentation
In the CQV process, thorough documentation is key to compliance, traceability, and future reviews. It is vital to ensure that all activities related to IQ, OQ, and PQ are properly documented with accurate details. All validation activities should be logged meticulously, as these documents are subject to inspection during regulatory audits.
Using standardized templates and ensuring that documentation aligns with the regulatory guidelines can reduce the risk of errors. Documentation should include installation protocols, operational qualifications, performance results, and any other related activities that demonstrate the CQV process has been completed correctly. Remember, consistency and accuracy in documentation not only satisfy regulatory bodies but also provide a valuable reference for future activities or requalification needs.
5. Leverage Digital Tools for Efficiency
Technology plays a critical role in improving the reliability and efficiency of the CQV process. Utilizing digital tools can streamline many of the manual processes that typically take up significant time and resources. Software tools designed for validation management can help automate progress tracking, reduce human error, and ensure that validation activities are conducted in real-time.
Electronic documentation systems, cloud-based platforms, and even IoT-enabled monitoring devices can all contribute to more efficient and accurate CQV processes. These tools allow for real-time data collection, better collaboration between teams, and faster access to key documentation. By incorporating such technologies, you can significantly enhance the overall efficiency and reliability of your CQV results.
6. Engage Cross-Functional Teams
CQV requires collaboration between various departments, including engineering, quality assurance, and production. Effective communication and a shared understanding of objectives among these teams are essential for achieving reliable CQV results.
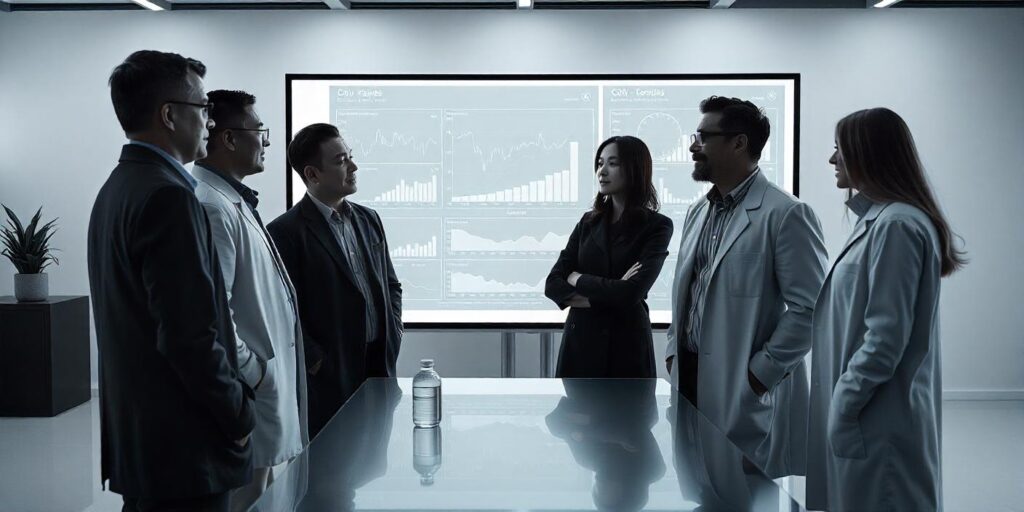
Having a cross-functional approach ensures that all departments involved in the process are on the same page and aware of their respective responsibilities. Regular team meetings, clear communication channels, and coordination between departments help mitigate misunderstandings and ensure that every step of the CQV process is executed flawlessly. When teams work in silos, the potential for errors increases, ultimately impacting the final results of the CQV process.
7. Conduct Preemptive Testing
Before embarking on formal validation activities, it’s essential to conduct preliminary or preemptive testing. This can include simulations, dry runs, or initial trials that help identify potential issues early in the process. Performing preemptive testing helps to fine-tune protocols and detect flaws in the system that may not have been anticipated.
For example, equipment calibration or environmental factors such as temperature fluctuations can affect validation outcomes. By addressing these challenges in the early stages, you can avoid delays during IQ, OQ, and PQ activities, ultimately ensuring the reliability of your results.
8. Adopt a Lifecycle Approach
CQV is an ongoing process that doesn’t stop once a product or system is validated. To ensure continued compliance and efficiency, adopting a lifecycle approach is critical. Regular reviews, requalification, and continuous monitoring of equipment and processes are necessary to ensure that they remain in a validated state over time.
For instance, equipment calibration schedules should be regularly reviewed and updated, and any changes in the environment or production processes should trigger revalidation activities. By adopting this lifecycle approach, you ensure that CQV remains a dynamic process that adapts to changes, new technologies, or evolving regulatory requirements.
Read More: 6 Things to Know When You Are Choosing Your Compliance Partner
9. Emphasize Change Management
Change management is essential to maintaining the integrity of the process. Any changes made to equipment, processes, or systems must be properly evaluated for their impact on validation. Implementing a robust change management system ensures that every modification is tracked and assessed to determine if it requires requalification or further validation steps.
Changes, whether due to new equipment, updated software, or altered manufacturing processes, should always be followed by a detailed impact assessment. This ensures that the CQV outcomes remain reliable and compliant with regulatory standards, even in the face of evolving business needs or technological advancements.
10. Prepare for Regulatory Audits
Regulatory audits are an inevitable part of the CQV process. The preparation for such audits should start long before the inspection itself. Ensuring that your team is consistently following proper procedures and keeping accurate documentation is crucial to passing audits with minimal issues.
Key areas to focus on for audit readiness include:
- Validation records for IQ, OQ, and PQ activities.
- Logs of training and competency assessments for personnel involved.
- Detailed change control logs.
- Documentation of corrective actions taken when issues were identified.
A well-prepared audit process demonstrates to regulatory bodies that your validation activities are rigorous, traceable, and compliant with the necessary guidelines.
Read More: CQV: 6 Crucial Truths Every Pharma Professional Should Know
How Incepbio Can Help you
At Incepbio, we understand that the CQV process can be daunting, which is why we offer comprehensive support for your CQV needs. We specialize in providing:
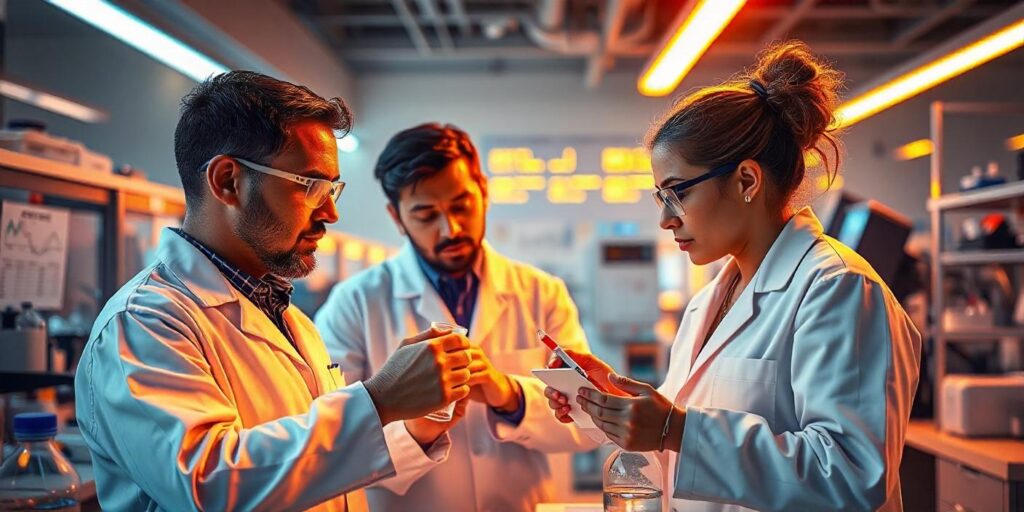
- End-to-End Support: We can assist in developing your validation Master Plan and execute validation activities with precision.
- Regulatory Expertise: Our team has in-depth knowledge of regulatory requirements, including FDA, EMA, and ISO standards, to ensure that your processes comply with the latest guidelines.
- Advanced Tools: We integrate cutting-edge digital solutions to optimize your CQV workflow and improve data accuracy.
- Comprehensive Documentation: We ensure that all validation steps are thoroughly documented, meeting both internal and external audit requirements.
Partnering with Incepbio ensures that your CQV process is streamlined, efficient, and always audit-ready, giving you peace of mind and a path to consistent regulatory compliance. To learn more about our services, visit here.
Conclusion
Reliable CQV results are critical for the success of your product development and manufacturing processes. By implementing these 10 practical tips, you can significantly improve your outcomes, ensuring that your systems are validated, compliant, and ready for use.
Whether you are just beginning your CQV journey or looking to optimize your existing processes, Incepbio is here to provide expert support every step of the way. Reach out to us today to discuss how we can help you achieve reliable and compliant results.
Authors
-
Shubhankar is a pharmaceutical professional with over 10 + years of experience in Drug Substance (Upstream), Aseptic Batch Manufacturing (Drug Product), Process Validation, and CQV (Commissioning, Qualification, and Validation). He is skilled in managing the qualification and implementation of protocols for URS, DQ, FAT, SAT, IQ, OQ, and PQ for new equipment. Holds sounds knowledge of CSV (Computer System Validation) in compliance with 21 CFR 210/211, 21 CFR Part 11, and European regulations. Shubhankar is experienced in creating cGMP-oriented documentation, including SOPs, BPRs, Calibration Records, and deviation investigations. Expertise in overseeing various validation activities, such as HVAC, Utility, and Process Equipment Validation.
View all posts -
An experienced SEO professional, Adithya is someone fascinated by the art of content creation. He has published over 700 articles under his name. Additionally, he has worked for companies like TCS, Essentially Sports, and holds expertise in the field of digital marketing
View all posts -
Arjun Jha has over 8 years of experience in tech startups, business strategy, and digital and traditional marketing. He’s helped many startups grow by using creative strategies and a deep understanding of the market. Outside of work, Arjun enjoys reading about business, philosophy, psychology, and spirituality, which inspires his unique approach to problem-solving and growth.
View all posts