Thermal validation is a critical process to ensure that temperature-sensitive products, such as pharmaceuticals, biologics, and medical devices, are stored, transported, and manufactured under proper conditions. Reliable thermal validation results are essential for regulatory compliance, product integrity, and customer safety. In this blog, we’ll provide 10 practical tips for ensuring your thermal validation process delivers accurate, reliable, and repeatable results.
1. Define Clear Validation Objectives
Before starting any thermal validation project, it’s important to clearly define your objectives. Are you validating storage conditions, transport conditions, or a manufacturing process? Establishing your goals upfront helps ensure that the right data is collected and that validation is performed according to the required standards.
Example: If you’re validating the storage conditions for a pharmaceutical product, your objectives might include maintaining a specific temperature range (e.g., 2–8°C) and ensuring that deviations are minimized to ensure product stability.
Read More: Thermal Validation: 8 Critical Regulatory Standards You Must Know
2. Select the Right Monitoring Equipment
Choosing the appropriate temperature monitoring equipment is crucial for obtaining reliable results. The instruments should be accurate, reliable, and suitable for the specific environment you’re testing. Additionally, they should be calibrated regularly to ensure they provide precise data.
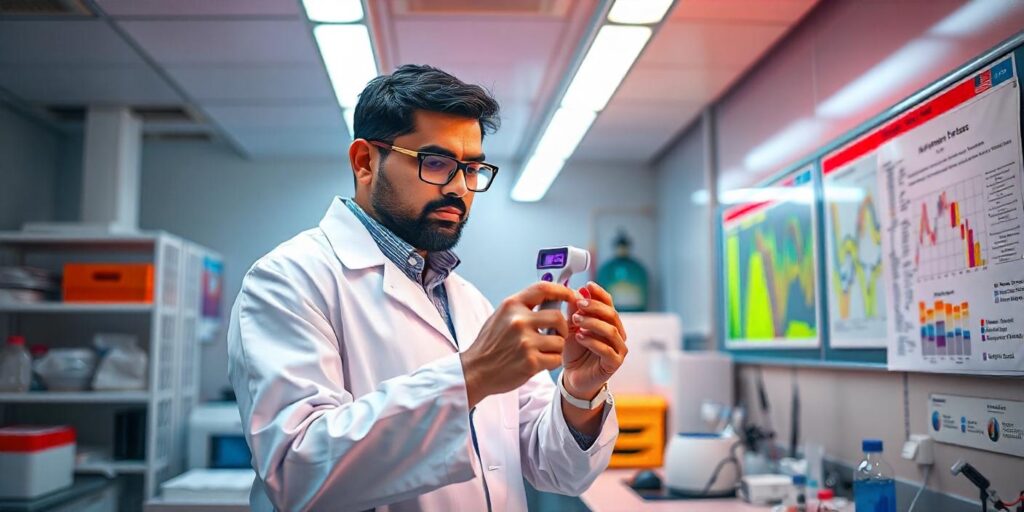
Example: For validating a transport container for temperature-sensitive drugs, you might choose data loggers with a high degree of accuracy and the ability to withstand environmental fluctuations during transit.
3. Plan for the Worst-Case Scenario
Consider worst-case scenarios when planning your thermal validation. This includes factors like power failures, equipment malfunctions, or extreme environmental conditions. Understanding how these scenarios could affect your product will allow you to incorporate buffer zones or additional safeguards during validation.
Example: If you’re validating a cold chain transport process, consider potential delays in transport or unexpected temperature spikes and include these conditions in your validation to ensure the product remains within the acceptable temperature range.
Read More: Top 10 Challenges in Thermal Validation and How to Overcome Them
4. Use Multiple Temperature Sensors
In some cases, using just one temperature sensor may not provide a full picture of the environment being validated. It’s often best to use multiple sensors at different locations within the validated area or system. This helps ensure that temperature variations are accounted for and that the results are more reliable.
Example: For validating a cold storage room, place sensors at key locations like the center, corners, and near the doors, as temperature can vary across the room. This provides a comprehensive assessment of the entire area.
5. Validate Over a Sufficient Period
Thermal validation should be conducted over a period of time to account for fluctuations and ensure that the system can maintain temperature control consistently. The duration of the validation depends on the nature of the product and the specific conditions you are testing.
Example: When validating a freezer for biologics, conducting a 24- to 48-hour validation may help capture any short-term temperature deviations that could compromise the product.
Read More: Thermal Validation: 5 New Cutting-Edge Technologies
6. Establish Clear Acceptance Criteria
Having clear and defined acceptance criteria is crucial for determining whether your thermal validation is successful. Establish thresholds for acceptable temperature ranges and tolerances, and ensure that all stakeholders are aware of these criteria before the validation process begins.
Example: In the case of validating a refrigerated transport system for vaccines, you might set an acceptable temperature range of 2–8°C, with an allowable deviation of ±0.5°C, based on product specifications.
7. Perform a Risk Assessment
Before starting thermal validation, conduct a risk assessment to identify potential hazards or areas of concern. A risk assessment will help you prioritize the areas that require the most attention and ensure that the thermal validation process addresses critical temperature control factors.
Example: In validating a warehouse for sterile medical devices, assess potential risks such as temperature fluctuations due to HVAC system failures, which could compromise product sterility. Use that information to improve system design or add additional temperature monitoring.
8. Account for Environmental Factors
Environmental factors, such as humidity, air circulation, and seasonal temperature variations, can impact thermal validation results. Be sure to monitor these variables and incorporate them into your validation process.
Example: For thermal validation of a temperature-sensitive product being shipped in varying climates, consider external factors like ambient temperatures and humidity during different seasons, which can affect the product during transit.
9. Document Everything Thoroughly
Accurate and comprehensive documentation is critical to ensuring that your thermal validation results are reliable and comply with regulatory standards. Keep detailed records of all procedures, calibration certifications, temperature data, and any deviations or corrective actions.
Example: When performing thermal validation for a pharmaceutical cold storage unit, document the locations of temperature sensors, calibration details for each sensor, and all temperature data points collected during the validation period. This will be necessary for audits and inspections.
10. Review and Analyze Data Carefully
Once the thermal validation process is complete, carefully analyze the data to identify any trends, anomalies, or areas of concern. This analysis will help you determine whether the validation was successful and if corrective actions are needed to ensure product integrity.
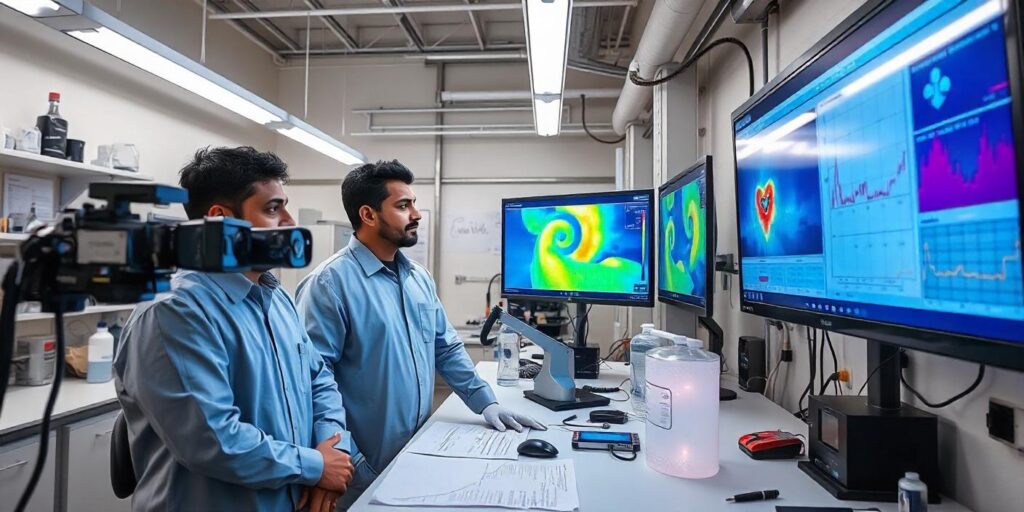
Example: After validating the temperature conditions in a sterile compounding pharmacy, review the data to see if any temperature deviations exceeded the acceptable threshold. If they did, investigate potential causes, such as equipment failure or improper insulation, and take corrective action.
Read More: 8 Mistakes to Absolutely Avoid While Performing Thermal Validation
Conclusion
Thermal validation is an essential process for ensuring the integrity of temperature-sensitive products, and reliable validation results are key to regulatory compliance, product safety, and customer satisfaction. By following these 10 practical tips, you can improve the accuracy and reliability of your thermal validation efforts and ensure that your temperature-controlled environments are operating optimally.
At Incepbio, we offer expertise in thermal validation, providing you with the tools and knowledge to meet regulatory requirements, maintain product integrity, and achieve reliable results. Whether you’re validating storage conditions, transport systems, or manufacturing processes, Incepbio is here to guide you every step of the way.
For more information or to discuss your thermal validation needs, contact Incepbio today!
Authors
-
-
Arjun Jha has over 8 years of experience in tech startups, business strategy, and digital and traditional marketing. He’s helped many startups grow by using creative strategies and a deep understanding of the market. Outside of work, Arjun enjoys reading about business, philosophy, psychology, and spirituality, which inspires his unique approach to problem-solving and growth.
View all posts -
An experienced SEO professional, Adithya is someone fascinated by the art of content creation. He has published over 700 articles under his name. Additionally, he has worked for companies like TCS, Essentially Sports, and holds expertise in the field of digital marketing
View all posts