Commissioning, Qualification, and Validation (CQV) can feel like navigating a maze of compliance requirements, technical standards, and detailed processes. For pharmaceutical and medical device manufacturers, successful CQV ensures product quality, regulatory compliance, and ultimately, patient safety. However, the process can also present unique challenges. Mistakes along the way are common but can lead to costly setbacks, delays, and even regulatory issues.
In this blog, we’ll outline eight common mistakes that companies often overlook—and more importantly, how to avoid them. Let’s dive into these pitfalls and ensure your CQV process runs smoothly.
Why Avoiding Mistakes in CQV Matters
When it comes to CQV, precision is crucial. Even minor missteps can lead to regulatory risks, non-compliance, or compromised product quality. By understanding and avoiding these common mistakes, companies can protect their operations, prevent costly errors, and maintain high standards that set them apart in the industry.
1. Skipping Preliminary Risk Assessment
A thorough risk assessment is the foundation of any effective CQV process. Without this step, it’s like starting a journey without a map. Risk assessments help identify potential issues early on, saving time, money, and resources.
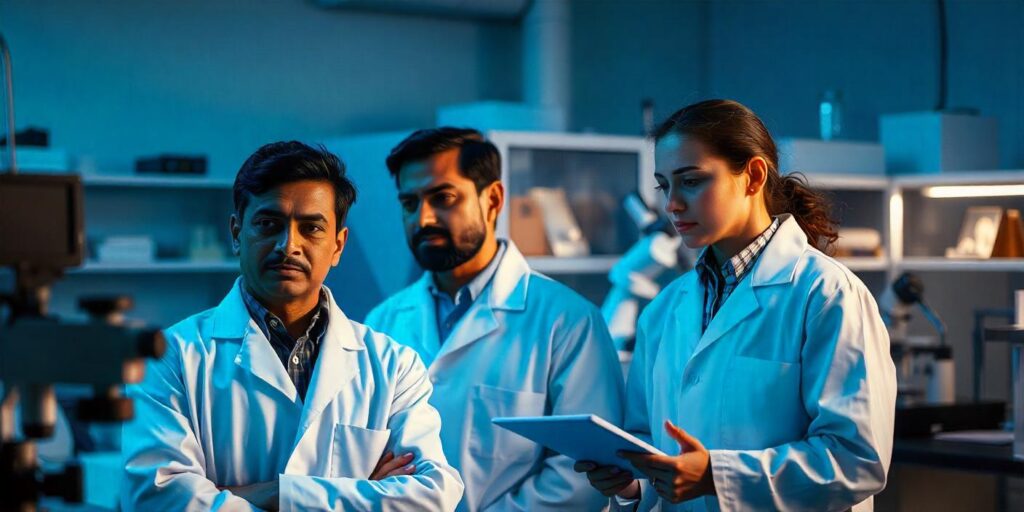
- Why It’s Important: Without a risk assessment, hidden risks can cause unforeseen challenges, resulting in costly rework or even compliance failures.
- Solution: Conduct a detailed risk assessment at the beginning of each project. This allows your team to address risks proactively and prevent future issues.
2. Incomplete Documentation Processes
When documentation is incomplete or disorganized, it’s like building a house with no blueprint. Regulatory agencies rely on clear, detailed documentation to verify compliance. Missing documents or inconsistent records can lead to issues during audits or inspections.
- Why It’s Important: Incomplete documentation affects traceability and compliance, making it harder to track CQV processes and provide evidence of adherence to standards.
- Solution: Standardize your documentation process. Use templates, checklists, and guidelines to ensure all activities are consistently recorded. This saves time and minimizes errors.
3. Failing to Train Personnel on CQV Protocols
CQV is a complex process, and everyone involved needs to understand their role. Without adequate training, even the best-designed process can fall short.
- Why It’s Important: When personnel aren’t properly trained, they’re more likely to skip steps or overlook important details, jeopardizing compliance.
- Solution: Schedule regular training sessions on CQV protocols for everyone involved. This ensures that your team understands the process, reducing the risk of errors and improving overall efficiency.
4. Overlooking Data Integrity
Data integrity is crucial for compliance and operational accuracy. If data is incomplete, inaccurate, or altered, it compromises the entire CQV process.
- Why It’s Important: Regulatory bodies like the FDA and and EMA emphasize data integrity, and issues in this area can lead to audits, fines, or worse.
- Solution: Use validated software systems with secure audit trails to manage CQV data. Regular audits of data entry and storage procedures ensure that data remains accurate and traceable.
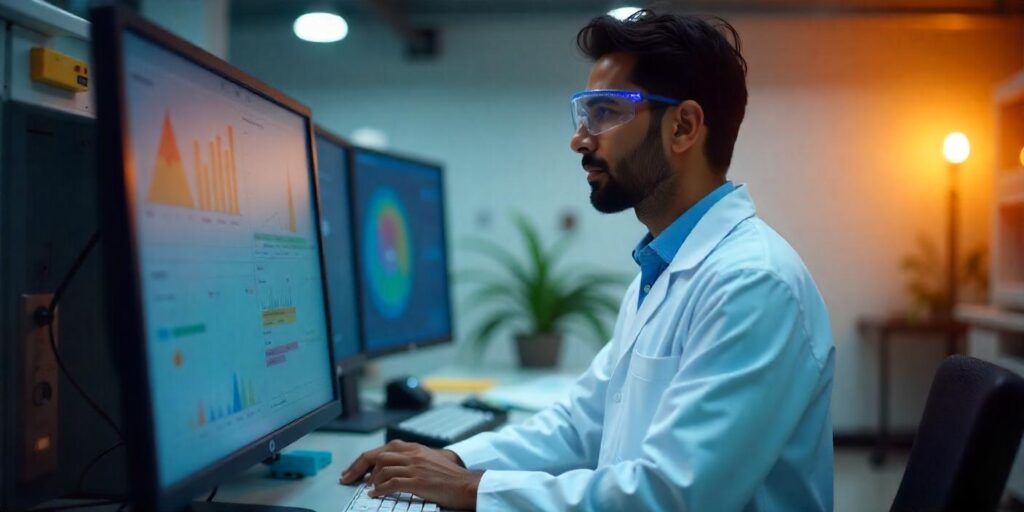
5. Ignoring Regular Maintenance and Requalification
Once systems and equipment are validated, they require ongoing maintenance and requalification to ensure they stay compliant. Neglecting this can lead to performance issues and non-compliance.
- Why It’s Important: Without regular requalification, equipment may no longer meet validated states, which can affect product quality and safety.
- Solution: Develop a maintenance and requalification schedule that aligns with your CQV plan. Regular checks help ensure that everything stays up to regulatory standards.
6. Relying on Outdated Procedures
The pharmaceutical and medical device industries are constantly evolving, with regulatory bodies frequently updating standards. Using outdated procedures can mean falling behind on compliance requirements.
- Why It’s Important: Regulatory standards change, and outdated practices may no longer be compliant. Failing to update processes can lead to penalties or rework.
- Solution: Keep your CQV procedures current by regularly reviewing and updating them to match industry standards. Assign a team member to monitor regulatory updates and ensure processes align with the latest requirements.
Read More: 8 Dangerous Myths About CQV Holding Your Company Back – And How to Break Free for Success!
7. Inadequate Testing of Systems and Processes
Thorough testing is key to verifying that systems function as expected. Skipping or rushing testing can mean missing critical errors, leading to process failures and product quality issues.
- Why It’s Important: Insufficient testing increases the risk of system malfunctions, which can impact product quality and compliance.
- Solution: Develop a testing plan that covers each CQV stage, from commissioning to validation. This ensures comprehensive checks and confirms system reliability before production begins.
8. Overlooking Environmental Control Factors
Environmental controls, such as temperature, humidity, and air quality, play a crucial role in ensuring product safety and compliance. Neglecting these factors can lead to contamination or degradation of products.
- Why It’s Important: Environmental factors directly impact product quality. Failing to control them can compromise product integrity and lead to regulatory issues.
- Solution: Monitor critical environmental parameters closely and set up strict controls in high-sensitivity areas like clean rooms. Regular checks and adjustments help maintain a controlled environment and prevent contamination.
How Incepbio Supports Your CQV Journey
At Incepbio, we understand that CQV is a challenging process, and we’re here to help every step of the way. From risk assessment to documentation support, training, and environmental control, our team at incepbio.com has the expertise and resources to streamline your process and ensure compliance.
Our CQV services include:
- Detailed Assessments: We conduct thorough CQV assessments to identify risks and optimize your processes, keeping you compliant with all regulatory requirements.
- Documentation Support: Our team assists with the organization and maintenance of CQV documentation, ensuring that every step is well-documented and audit-ready.
- Personnel Training: We offer training programs to equip your team with the knowledge and skills to manage CQV effectively, improving overall efficiency and compliance.
- Environmental Control Solutions: Our experts help monitor and regulate environmental factors to maintain product integrity and avoid contamination risks.
Read More: Avoiding Disaster: 3 Dangerous Pharmaceutical Compliance Mindsets
Incepbio’s support means a smoother CQV process, allowing you to focus on delivering high-quality products with confidence.
Final Words
Avoiding common CQV mistakes is essential for pharmaceutical and medical device manufacturers aiming to maintain compliance, quality, and operational efficiency. By recognizing and addressing these eight pitfalls, you can set your process up for success and avoid unnecessary delays and costs.
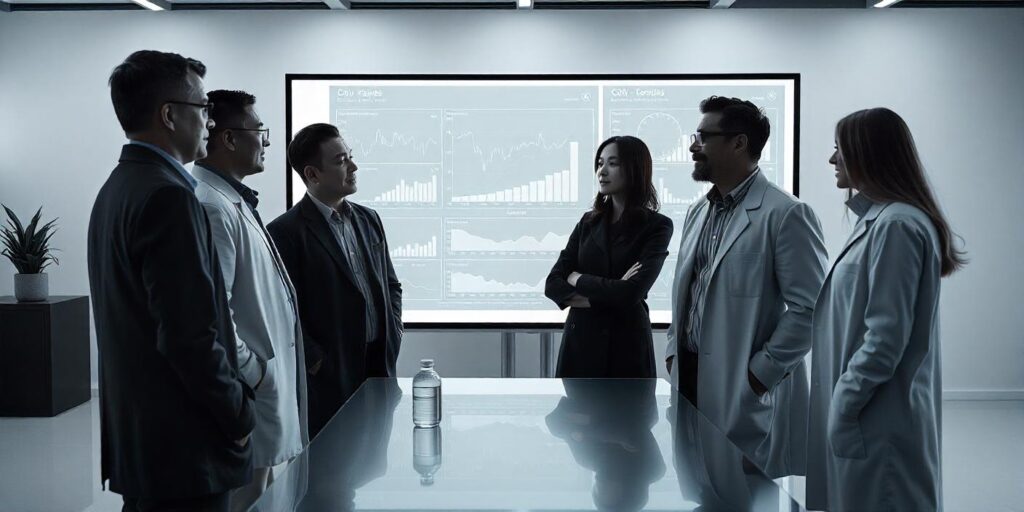
Partnering with Incepbio can provide the expertise and resources needed to navigate CQV challenges with confidence. By staying proactive, keeping your processes up-to-date, and investing in continuous improvement, you’ll achieve compliance and quality that give you a competitive edge in the market.
Authors
-
Shubhankar is a pharmaceutical professional with over 10 + years of experience in Drug Substance (Upstream), Aseptic Batch Manufacturing (Drug Product), Process Validation, and CQV (Commissioning, Qualification, and Validation). He is skilled in managing the qualification and implementation of protocols for URS, DQ, FAT, SAT, IQ, OQ, and PQ for new equipment. Holds sounds knowledge of CSV (Computer System Validation) in compliance with 21 CFR 210/211, 21 CFR Part 11, and European regulations. Shubhankar is experienced in creating cGMP-oriented documentation, including SOPs, BPRs, Calibration Records, and deviation investigations. Expertise in overseeing various validation activities, such as HVAC, Utility, and Process Equipment Validation.
View all posts -
An experienced SEO professional, Adithya is someone fascinated by the art of content creation. He has published over 700 articles under his name. Additionally, he has worked for companies like TCS, Essentially Sports, and holds expertise in the field of digital marketing
View all posts -
Arjun Jha has over 8 years of experience in tech startups, business strategy, and digital and traditional marketing. He’s helped many startups grow by using creative strategies and a deep understanding of the market. Outside of work, Arjun enjoys reading about business, philosophy, psychology, and spirituality, which inspires his unique approach to problem-solving and growth.
View all posts