Maintaining cleanroom hygiene is a cornerstone of quality assurance in the pharma industry. Cleanrooms are critical environments where stringent contamination controls ensure product integrity and patient safety. During the Commissioning, Qualification, and Validation (CQV) process, monitoring cleanroom hygiene becomes even more vital to meet regulatory standards and operational excellence.
This blog explores five key metrics that provide actionable insights into cleanroom hygiene during CQV processes. These metrics help organizations achieve compliance with cGMP guidelines, reduce contamination risks, and optimize cleanroom performance.
1. Airborne Particulate Levels (NVPC)
Why It Matters: Cleanroom classifications, as defined by ISO 14644 and other standards, are based on allowable airborne particulate levels. During CQV, measuring particulate concentrations ensures the cleanroom’s air handling systems are functioning as designed and maintaining the required cleanliness levels. This is critical for ensuring product safety and maintaining compliance with regulatory standards.
How to Measure:
- Use particle counters: Measure airborne particles in critical zones to assess air quality.
- Conduct testing in different states: Test during both at-rest and operational states to validate system performance under varying conditions.
- Benchmark against standards: Compare results against ISO class requirements or other applicable standards to ensure compliance.
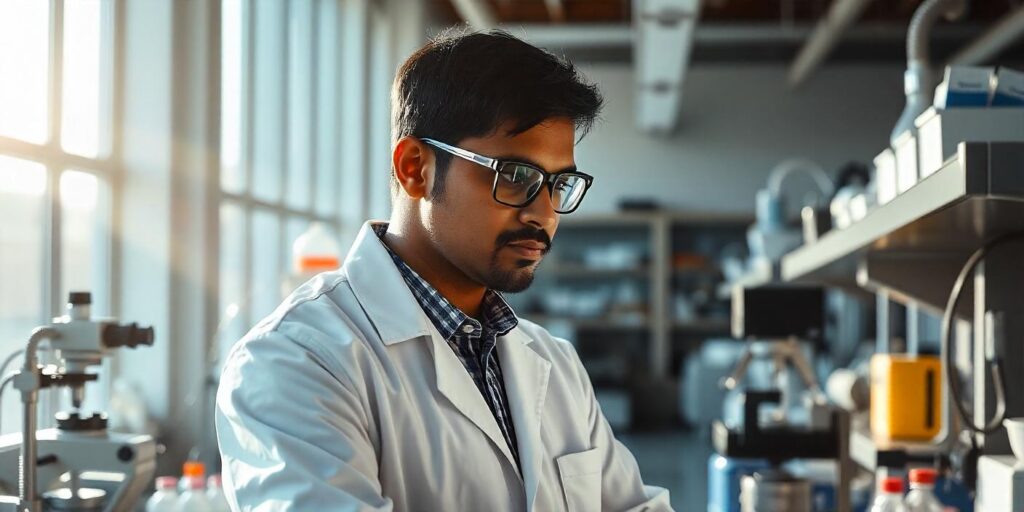
Recommended Action: If particulate levels exceed limits, take immediate action by:
- Investigating potential issues with air filtration systems.
- Evaluating HVAC system performance and filter integrity.
- Reviewing personnel practices and movement patterns within the cleanroom to identify contamination sources.
2. Microbial Contamination Levels (VPC)
Why It Matters: Microbial contamination poses a significant risk to sterile manufacturing processes. Monitoring microbial levels ensures that aseptic conditions are maintained throughout CQV, safeguarding both products and patient safety. High microbial loads can compromise product efficacy and lead to costly recalls.
Read More: 10 Burning Questions on CQV
How to Measure:
- Active air sampling: Use impaction devices to collect air samples and measure microbial load in real-time.
- Settle plate testing: Place settle plates in various locations to monitor microbial fallout over extended periods.
- Surface sampling: Collect swabs and contact plate samples from critical equipment and surfaces to identify contamination hotspots.
Recommended Action: If microbial counts exceed acceptable levels:
- Reassess cleaning protocols and frequency.
- Review and improve personnel gowning procedures.
- Evaluate the effectiveness of air filtration systems and make necessary upgrades.
3. Contact Plate Surface Cleanliness
Why It Matters: Surface contamination can act as a vector for both particulate and microbial contamination. Ensuring that all surfaces meet cleanliness standards during CQV validates the efficacy of cleaning protocols and minimizes the risk of cross-contamination.
How to Measure:
- ATP bioluminescence testing: Use ATP testing to detect organic residues on surfaces, providing real-time feedback on cleanliness.
- Chemical residue testing: Ensure that residues from cleaning agents are fully removed to prevent adverse reactions with products.
- Periodic swabbing: Analyze swabs taken from high-touch areas to identify recurring contamination issues.
Recommended Action: If residues or contaminants are detected:
- Revise cleaning procedures to target identified hotspots.
- Evaluate the performance and suitability of cleaning agents.
- Train personnel on improved cleaning techniques and protocols.
4. Differential Pressure Monitoring
Why It Matters: Maintaining proper differential pressure between cleanroom zones is essential to preventing cross-contamination. Pressure imbalances can compromise cleanroom integrity and allow contaminants to infiltrate critical areas.
How to Measure:
- Calibrated pressure gauges: Use high-precision sensors to monitor pressure differentials across cleanroom boundaries.
- Routine operational checks: Conduct pressure checks during operational simulations to ensure consistency.
- Baseline documentation: Record pressure readings regularly to establish a performance baseline and detect anomalies.
Recommended Action: If pressure imbalances are identified:
- Adjust HVAC systems, including airlocks and filters, to restore proper pressure cascades.
- Investigate potential leaks or obstructions in the airflow.
- Conduct further testing to confirm stability after adjustments.
Read More: CQV: 6 Crucial Truths Every Pharma Professional Should Know
5. Personnel Hygiene Compliance
Why It Matters: Personnel are a primary source of contamination in cleanrooms. Monitoring hygiene compliance during CQV ensures that gowning procedures, hand hygiene practices, and movement protocols are consistently followed, minimizing contamination risks.
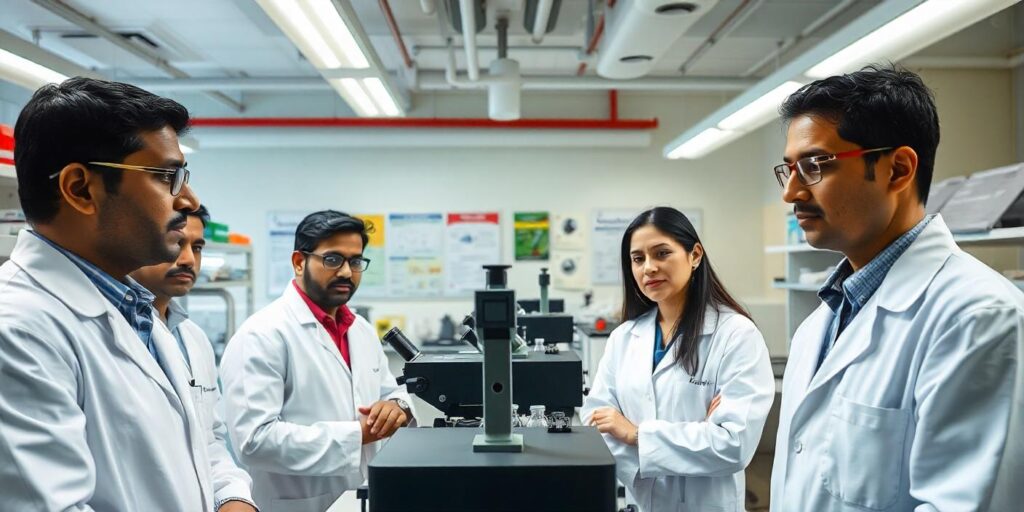
How to Measure:
- Microbial sampling: Test gloves and gown surfaces post-gowning to ensure proper hygiene.
- Visual and automated inspections: Monitor adherence to proper gowning sequences using manual or automated systems.
- Training evaluations: Conduct regular training sessions and assessments on hygiene protocols.
Recommended Action: If non-compliance is observed:
- Implement retraining programs to address knowledge gaps.
- Refine gowning protocols to improve adherence and ease of compliance.
- Enhance facility design to eliminate obstacles to proper hygiene practices, such as improving gowning areas or adding visual reminders.
How Incepbio Can Help with Your CQV Needs
At Incepbio, we specialize in providing comprehensive solutions to meet your CQV requirements. Our team of experts understands the critical role that cleanroom hygiene plays in ensuring regulatory compliance and operational excellence. Here’s how we can assist:
- Customized CQV Strategies: We tailor our CQV plans to align with your facility’s unique needs and industry standards, ensuring a seamless validation process.
- Expert Guidance: Our experienced professionals bring in-depth knowledge of cGMP guidelines, ISO standards, and the latest industry practices to ensure your cleanroom operations are validated to the highest standards.
- State-of-the-Art Testing: We utilize advanced technologies for monitoring airborne particulate levels, microbial contamination, surface cleanliness, and more to provide accurate and reliable results.
- Personnel Training: We offer comprehensive training programs to ensure your team is well-versed in cleanroom protocols, hygiene compliance, and best practices for contamination control.
- Continuous Support: From initial commissioning to ongoing validation, our support services ensure your cleanroom maintains optimal performance throughout its lifecycle.
Partnering with Incepbio means gaining a trusted ally dedicated to the success of your cleanroom operations. Let us help you achieve and maintain the highest standards of CQV compliance.
Investing in robust monitoring and adherence to these metrics during CQV will pave the way for long-term operational excellence and product integrity.
Read More: Understanding the Hidden Dangers of CQV
Conclusion
The CQV process is a pivotal phase in ensuring cleanroom operations meet the highest standards of hygiene and compliance. By closely monitoring these five key metrics – airborne particulate levels, microbial contamination, surface cleanliness, differential pressure, and personnel hygiene compliance – organizations can validate cleanroom performance effectively.
Each metric provides unique insights into potential contamination risks and areas for improvement. Leveraging these insights ensures that cleanroom environments not only meet regulatory standards but also support efficient and safe production processes.
Investing in robust monitoring and adherence to these metrics during CQV will pave the way for long-term operational excellence and product integrity.
Authors
-
Shubhankar is a pharmaceutical professional with over 10 + years of experience in Drug Substance (Upstream), Aseptic Batch Manufacturing (Drug Product), Process Validation, and CQV (Commissioning, Qualification, and Validation). He is skilled in managing the qualification and implementation of protocols for URS, DQ, FAT, SAT, IQ, OQ, and PQ for new equipment. Holds sounds knowledge of CSV (Computer System Validation) in compliance with 21 CFR 210/211, 21 CFR Part 11, and European regulations. Shubhankar is experienced in creating cGMP-oriented documentation, including SOPs, BPRs, Calibration Records, and deviation investigations. Expertise in overseeing various validation activities, such as HVAC, Utility, and Process Equipment Validation.
View all posts -
-
An experienced SEO professional, Adithya is someone fascinated by the art of content creation. He has published over 700 articles under his name. Additionally, he has worked for companies like TCS, Essentially Sports, and holds expertise in the field of digital marketing
View all posts