In the high-stakes world of pharmaceutical and medical device manufacturing, keeping equipment safe is paramount. Commissioning, Qualification, and Validation (CQV) aren’t just technical buzzwords—they’re your foundation for ensuring that your equipment meets the highest standards for safety and reliability. But navigating the process isn’t always simple. From validation to maintaining compliance, you face numerous challenges.
This blog reveals seven insider secrets tailored to protect your equipment and streamline your operations. We’ll break down each step to show you how CQV can shield your business from risks, reduce downtime, and ensure regulatory compliance. Let’s dive into the solutions that can make a difference in your processes.
What Is CQV, and Why Is It Essential for Equipment Safety?
Commissioning, Qualification, and Validation is a structured approach to ensure your equipment is safe and functions as intended. Each component—Commissioning, Qualification, and Validation—plays a unique role in assessing, verifying, and maintaining your equipment’s integrity.
In this industry, equipment safety is non-negotiable. Reliable validation practices protect your product quality and patient safety, so understanding how CQV works is the first step to safeguarding your operations.
Read More: Common Mistakes to Avoid During Commissioning, Qualification, and Validation
Why Investing in commissioning, qualification, and validation Saves Money Over Time
Though CQV may seem like a significant investment initially, proactive practices can save you substantial costs in the long run. Preventative measures, such as regular validation, calibration, and maintenance helps you avoid equipment breakdown and production halts. For example, scheduling regular inspections and predictive maintenance can prevent equipment from reaching critical failure points, minimizing expensive emergency repairs or replacements.
How it Reduces Regulatory Fines and Compliance-Related Expenses
Non-compliance with regulatory standards like FDA’s cGMP or ISO 13485 can lead to hefty fines, costly recalls, or even production shutdowns. By embedding necessary protocols into your operations, you’re staying ahead of compliance requirements and avoiding penalties. Having documented CQV processes in place provides clear evidence of compliance during audits, further protecting your bottom line.
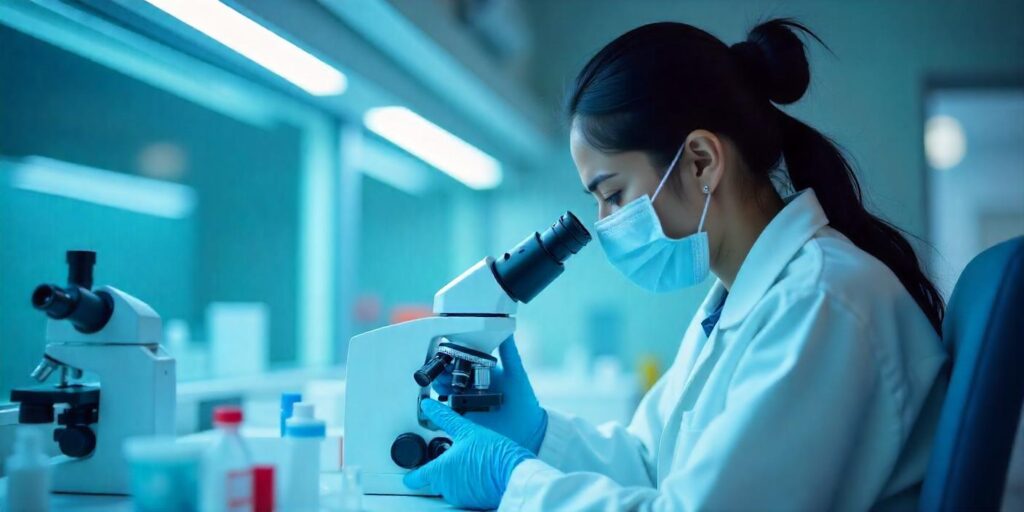
A proactive approach ensures that your equipment remains in optimal condition, extending its life span and maximizing your investment in manufacturing tools.
The 7 Secrets of Effective CQV to Ensure Equipment Safety
1. Defining Clear CQV Protocols Reduces Equipment Risk
Having well-defined protocols keeps your processes organized and reduces risks. With set guidelines, you prevent errors, avoid miscommunication, and maintain compliance with standards such as the FDA’s cGMP (Current Good Manufacturing Practice).
2. Risk-Based Assessments Enhance Equipment Longevity
CQV isn’t one-size-fits-all; using risk-based assessments allows you to prioritize equipment needing more rigorous validation. By focusing on higher-risk areas, you can extend your equipment’s lifespan and prevent costly downtime.
3. Preventative Maintenance Plans Work Best
Routine inspections, calibrations, and predictive maintenance keep equipment running smoothly. For instance, checking seals, filters, and tubing regularly prevents small issues which could lead to big problems. A regular maintenance plan reduces emergency repairs and saves costs in the long run.
4. Use Data-Driven Insights for CQV Optimization
Collecting and analyzing data, such as performance metrics,maintenance logs and history cards allows you to spot trends and anticipate issues. For example, monitoring pressure and temperature readings over time helps you detect gradual changes, preventing sudden failures. Leveraging data enables more proactive, precise management.
Read More: 7 Tips to Train Your Team Better on CQV Compliance
5. Training and Expertise Are Crucial for Successful CQV Implementation
It’s not just about the equipment; trained personnel are critical for success. Conducting regular training sessions ensures your team understands and follows best practices, reducing the likelihood of human error. Imagine the peace of mind knowing that everyone handling your equipment is well-trained.
6. Role of Documentation in Equipment Safety Through CQV
Documentation is your best friend when it comes to audits and compliance. Accurate records of every maintenance, inspection, and test provide traceability and accountability, helping you prove compliance with standards like ISO 13485 (for medical devices) and GMP.
7. Validation Testing and Re-qualification Support Long-Term Equipment Safety
CQV isn’t a one-time process; periodic validation testing and re-qualification ensure that equipment continues to perform as expected. For example, conducting annual re-validation checks allows you to identify any issues early,rectify them and maintain consistent equipment quality and performance.
Read More: CQV: 6 Crucial Truths Every Pharma Professional Should Know
Why Is Ongoing CQV Critical for Compliance and Regulatory Assurance?
Staying compliant means keeping up with evolving regulations, such as updates from the FDA and EMA. These agencies emphasize continuous validation and regular reviews, so your CQV program must be adaptable and proactive.
How Does CQV Compliance Build Trust with Stakeholders and Clients?
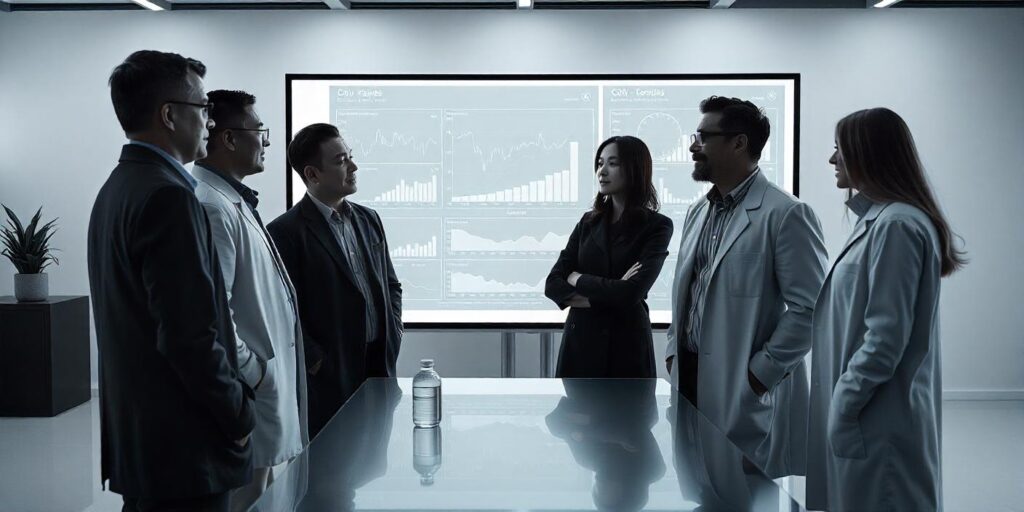
Transparent, reliable CQV processes enhance your credibility with clients and regulatory bodies. When you prioritize equipment safety, you’re showing clients that quality and compliance are non-negotiable. It’s a powerful way to build trust and set yourself apart in the industry.
What Are the Most Common CQV Pitfalls and How Can You Avoid Them?
Implementing CQV can be complex, and there are common pitfalls that even seasoned professionals may overlook. For example, inconsistent documentation is a frequent issue, as it leads to gaps in compliance and makes audits challenging. Another pitfall is neglecting to update protocols as regulations evolve or as equipment undergoes changes over time.
How to Avoid These CQV Pitfalls with Best Practices
To avoid these traps, ensure that documentation processes are standardized, with regular audits to catch and fix inconsistencies. Additionally, establish a schedule for reviewing and updating your CQV protocols so they remain aligned with current regulatory requirements and any modifications in your equipment or operations. By staying proactive and detail-oriented, you can navigate around these pitfalls and keep your program running smoothly.
Identifying and addressing these common pitfalls early on will save time, reduce risk, and enhance the overall effectiveness of your program.
How Incepbio Can Assist You
At Incepbio, we specialize in helping companies like yours implement effective CQV strategies. Our experts provide guidance, training, and support to help you establish robust processes that meet regulatory standards. We offer customized solutions to streamline your CQV approach and keep your equipment safe.
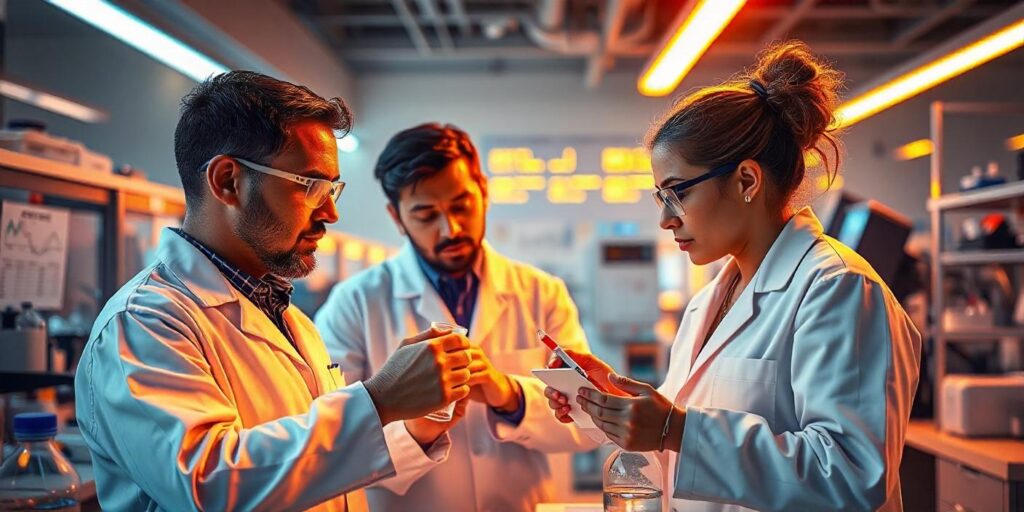
With Incepbio by your side, you can be confident in your practices, knowing they’re optimized for safety, compliance, and efficiency.
Conclusion
CQV is essential for ensuring the safety, reliability, and compliance of your equipment. By implementing the seven secrets we’ve outlined, you can protect your equipment, minimize risks, and keep operations running smoothly. Remember, validation isn’t just about checking boxes; it’s about fostering a culture of quality and safety.
If you’re ready to enhance your validation strategy, Incepbio is here to help. Our team can guide you in building a strong CQV framework, ensuring that your equipment stays safe, compliant, and ready for anything.
Authors
-
Shubhankar is a pharmaceutical professional with over 10 + years of experience in Drug Substance (Upstream), Aseptic Batch Manufacturing (Drug Product), Process Validation, and CQV (Commissioning, Qualification, and Validation). He is skilled in managing the qualification and implementation of protocols for URS, DQ, FAT, SAT, IQ, OQ, and PQ for new equipment. Holds sounds knowledge of CSV (Computer System Validation) in compliance with 21 CFR 210/211, 21 CFR Part 11, and European regulations. Shubhankar is experienced in creating cGMP-oriented documentation, including SOPs, BPRs, Calibration Records, and deviation investigations. Expertise in overseeing various validation activities, such as HVAC, Utility, and Process Equipment Validation.
View all posts -
An experienced SEO professional, Adithya is someone fascinated by the art of content creation. He has published over 700 articles under his name. Additionally, he has worked for companies like TCS, Essentially Sports, and holds expertise in the field of digital marketing
View all posts -
Arjun Jha has over 8 years of experience in tech startups, business strategy, and digital and traditional marketing. He’s helped many startups grow by using creative strategies and a deep understanding of the market. Outside of work, Arjun enjoys reading about business, philosophy, psychology, and spirituality, which inspires his unique approach to problem-solving and growth.
View all posts