Thermal validation is an essential process across several industries, including pharmaceuticals, medical devices, and food production. However, there are numerous myths surrounding this process that can lead to confusion and costly mistakes. In this blog, we’ll debunk the top 7 myths in thermal validation and clarify the truths behind them, helping you to make better-informed decisions for your validation process.
Myth 1: Thermal Validation is Only About High-Temperature Environments
The Truth: Thermal validation applies to both high and low-temperature environments.
Many people assume thermal validation is only relevant in scenarios involving high temperatures, such as autoclaving or sterilization processes. However, cold storage environments (such as refrigerators and freezers) also require validation to ensure the temperature remains within safe and effective ranges for products.
Why It Matters: Extreme temperatures, whether hot or cold, can lead to product degradation or compromise the quality and safety of sensitive materials. Validation ensures that both ends of the temperature spectrum are accounted for and that your product is always stored or processed at the optimal temperature.
What to Do:
- Perform thermal validation for all temperature-controlled environments, including cold storage.
- Test equipment in both high and low-temperature ranges to meet the needs of your specific process.
Read More: Thermal Validation: 8 Critical Regulatory Standards You Must Know
Myth 2: Thermal Validation is Only Required Once
The Truth: Thermal validation is an ongoing process that needs regular revalidation.
A common misconception is that thermal validation is a one-time event and doesn’t require ongoing attention. In reality, as systems age, equipment wears out, and processes change, revalidation is crucial to ensure that temperature control remains consistent.
Why It Matters: Failure to revalidate can result in unnoticed temperature fluctuations, which could affect product quality or safety. Without revalidation, you risk compliance failures and compromised product integrity.
What to Do:
- Implement regular revalidation schedules based on industry standards and regulatory requirements.
- Periodically inspect temperature monitoring equipment to ensure that it continues to function accurately.
Myth 3: Temperature Monitoring is Sufficient for Thermal Validation
The Truth: Temperature monitoring alone does not provide a complete picture of thermal validation.
Monitoring temperature is just one component of thermal validation. While it’s important, other factors, such as temperature uniformity, the equipment’s calibration, and the thermal performance of the entire system, must also be validated to ensure the conditions are consistent and reliable.
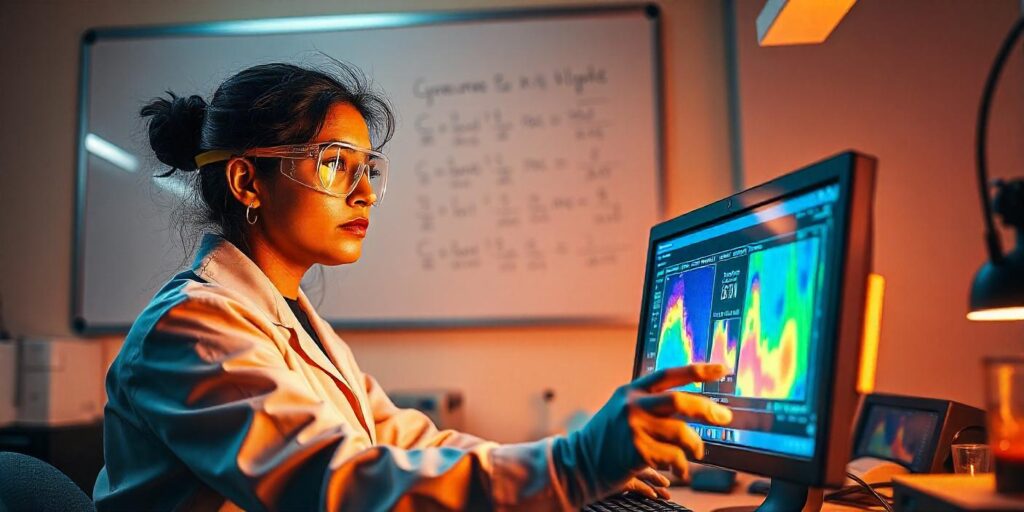
Why It Matters: Temperature alone may not tell you the full story about whether your system is operating correctly. Hot or cold spots, uneven distribution of temperature, and equipment malfunctions can lead to problems that go unnoticed if you only monitor temperature.
What to Do:
- Assess temperature uniformity and distribution by placing sensors in multiple locations.
- Validate the equipment and systems as a whole, ensuring they maintain consistent temperature throughout the entire process.
Read More: 6 Essential Parameters to Evaluate Before Selecting Validation Equipment
Myth 4: Only the Temperature at the Center of the Room Needs to Be Measured
The Truth: Temperature should be measured at multiple locations to ensure uniformity.
It’s a common myth that measuring the temperature at the center of the room or chamber is sufficient to validate a thermal system. In reality, temperature distribution can vary significantly throughout the room, with certain areas being hotter or colder than others.
Why It Matters: By measuring temperature at only one location, you may miss areas that don’t meet the required standards. Hot or cold spots can compromise the quality of the product and lead to compliance issues.
What to Do:
- Use multiple temperature sensors in different parts of the room or system to monitor temperature variation.
- Ensure that validation tests reflect the real-world conditions in which the products are processed or stored.
Myth 5: It is Only for Large-Scale Production Systems
The Truth: Thermal validation is important for both large and small-scale systems.
Some people assume that thermal validation is only necessary for large-scale industrial processes. However, small-scale systems, such as laboratory environments or smaller production facilities, can also be affected by temperature variations, which can influence the product’s quality and compliance status.
Why It Matters: Temperature control is vital for all types of production, not just large-scale operations. Even minor temperature fluctuations in smaller systems can affect product stability, safety, and regulatory compliance.
What to Do:
- Ensure that all systems, regardless of size, undergo proper thermal validation.
- Tailor the validation process to the specific scale and requirements of your system.
Myth 6: You Can Validate Thermal Conditions Without Considering External Environmental Factors
The Truth: External factors, such as humidity and air flow, can significantly affect thermal validation.
Some may believe that only the internal temperature of a system or room is relevant when validating thermal conditions. However, environmental factors, such as humidity, air circulation, and ambient temperature, can play a huge role in maintaining temperature stability and uniformity.
Why It Matters: Neglecting external factors could result in incomplete validation. Airflow patterns, humidity, and external temperature fluctuations can influence how effectively the thermal system maintains the target conditions, leading to inaccurate results.
What to Do:
- Consider environmental conditions, such as humidity and airflow, in your validation process.
- Test systems under real-world conditions to account for external variables.
Read More: Top 10 Challenges in Thermal Validation and How to Overcome Them
Myth 7: It is Too Expensive and Time-Consuming to Be Worth It
The Truth: While thermal validation requires investment, it’s an essential process for ensuring product quality, safety, and compliance.
Some may think thermal validation is a costly and time-consuming exercise that isn’t worth the effort. However, the cost of non-compliance—whether through regulatory fines, product recalls, or compromised quality—is far greater than the investment in a thorough thermal validation process.
Why It Matters: Not performing thermal validation can lead to serious consequences, including product failures, regulatory penalties, and damage to your reputation. The upfront investment is minimal compared to the long-term benefits of ensuring product quality and compliance.
What to Do:
- Understand the cost of non-compliance and weigh it against the benefits of thermal validation.
- Consider working with experts to streamline the process and ensure that your validation efforts are efficient and cost-effective.
Read More: Thermal Validation: 5 New Cutting-Edge Technologies
How Incepbio Can Help
Incepbio provides comprehensive thermal validation services that help ensure your systems meet industry standards and regulatory requirements. Whether you need assistance with temperature monitoring, equipment calibration, or environmental control, our team has the expertise and tools to support your thermal validation needs. Here’s how we can assist:
- Expert Guidance: We offer expert consultation to help you understand the best practices for your specific industry and requirements.
- Customized Validation Plans: We create tailored validation plans that meet your process needs, ensuring accuracy and compliance.
- Advanced Equipment: We use cutting-edge technology and monitoring systems to track temperature conditions accurately, ensuring your system is performing optimally.
- Detailed Documentation: We provide detailed reports and documentation that support audits and regulatory inspections.
- Ongoing Support: Our team provides ongoing support and revalidation services to ensure continuous compliance with thermal standards.
Conclusion
Thermal validation is an essential but often misunderstood process. By debunking these seven myths, we’ve clarified key aspects of thermal validation, from the importance of considering both high and low temperatures to the need for revalidation and external environmental factors. Understanding the truths about thermal validation can help you make informed decisions, ensure product safety, and meet regulatory requirements. Partner with Incepbio for your thermal validation needs, and ensure your systems are running at their best.