Thermal validation plays a critical role in ensuring the quality and safety of pharmaceutical and medical device products. Whether you’re designing a sterilization process or verifying the thermal properties of a facility, achieving the best results in thermal validation is essential to meet regulatory standards and maintain operational efficiency. In this blog, we will uncover eight secrets that can help you achieve optimal thermal validation results.
1. Understand the Regulatory Requirements
The first secret to successful thermal validation is understanding the regulatory requirements that apply to your industry. Thermal validation is governed by a variety of standards and guidelines, such as those set by the US FDA, ISO, and EU GMP. These regulations define the criteria for validating the thermal processes, whether for autoclaves, freeze-drying, or other sterilization equipment.
Be sure to stay up-to-date with the relevant regulations and ensure your validation process is compliant with them. Familiarizing yourself with the specific temperature ranges, dwell times, and other process parameters required by your regulatory body is essential for maintaining compliance and minimizing the risk of non-compliance.
2. Use Proper Calibration of Equipment
Accurate results in thermal validation are impossible without properly calibrated equipment. It is vital to calibrate your temperature sensors and monitoring equipment before initiating validation. Even small discrepancies in sensor readings can lead to inaccurate results and, ultimately, regulatory failure.
Read More: Top 10 Challenges in Thermal Validation and How to Overcome Them
Ensure that the calibration is performed regularly and in accordance with the manufacturer’s guidelines. Using certified calibration equipment and keeping a documented record of calibration activities will help ensure your results are trustworthy.
3. Map the Temperature Distribution
One of the most crucial aspects of thermal validation is mapping the temperature distribution within the system. Temperature mapping involves placing temperature sensors in various locations within the sterilization or process environment to ensure uniform heat distribution. Uneven heating can lead to under- or over-heating, compromising the sterilization process.
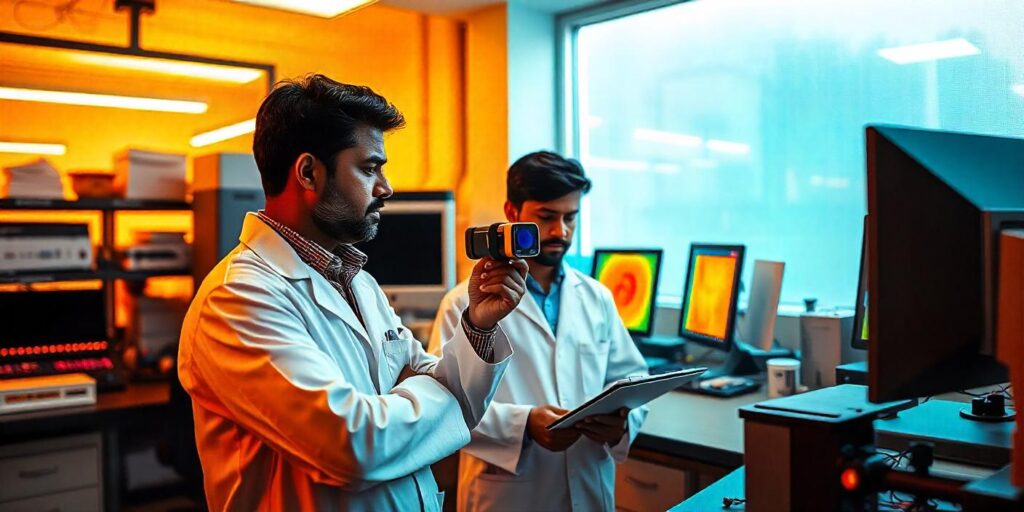
To map the temperature distribution accurately:
- Identify and place sensors in strategic locations within the equipment or chamber.
- Allow sufficient time for the system to reach a steady state.
- Analyze the data to ensure uniformity and correct hot spots if necessary.
Mapping the temperature distribution not only helps identify potential issues but also provides data that can be used to optimize the process.
4. Account for Product Load
The way your product is loaded into the system will impact how heat is distributed. Thermal validation should take into account the presence and configuration of the product load, as it can affect the heat transfer and temperature uniformity.
When validating processes like sterilization or pasteurization, ensure that the product load is properly arranged to allow even heat exposure. You should simulate real-world conditions as closely as possible during validation to ensure your results reflect the actual performance during normal operations.
Read More: Thermal Validation: 5 New Cutting-Edge Technologies
5. Determine the Correct Dwell Time
Dwell time refers to the amount of time the product or material is exposed to a particular temperature during the thermal process. Achieving the correct dwell time is essential for effective thermal validation. Too short of a dwell time can lead to insufficient sterilization, while too long can compromise the product quality.
You must determine the optimal dwell time by evaluating factors such as product type, material, and the specific thermal process. Conducting trials with different dwell times will allow you to fine-tune this parameter and ensure optimal results.
6. Perform Regular Re-qualification
Thermal validation is not a one-time event. Equipment and processes can change over time due to wear and tear, changes in the facility, or modifications in the product. Regular re-qualification of your thermal systems ensures that they continue to perform as expected and comply with regulatory standards.
Re-qualification should include checking the calibration of temperature sensors, verifying the temperature distribution, and assessing any changes in the process. Scheduling routine re-validation of your thermal systems will help maintain consistent performance and reduce the risk of operational failures.
7. Leverage Data Analysis for Optimization
The data collected during thermal validation is invaluable for both compliance and process optimization. Analyzing temperature data can help identify areas for improvement, optimize cycle times, and ensure that all components of the process are functioning as intended.
Read More: Thermal Validation: 8 Critical Regulatory Standards You Must Know
Advanced data analytics tools can be used to track temperature fluctuations, identify trends, and make adjustments in real-time. By leveraging data analysis, you can fine-tune your thermal processes and improve the efficiency and effectiveness of the system.
8. Partner with Experts
Thermal validation can be a complex and technically challenging process, especially when you are working with new equipment or products. Collaborating with experienced professionals who specialize in thermal validation can help streamline the process and ensure that all aspects of the validation are covered.
From designing the validation protocol to performing the necessary testing, having experts by your side ensures that the process is done efficiently and correctly. Partnering with a thermal validation expert can also help you navigate regulatory requirements, avoid common pitfalls, and ultimately achieve the best results.
Conclusion
Thermal validation is a critical component of ensuring product quality and regulatory compliance in the pharmaceutical and medical device industries. By following these eight secrets — understanding regulatory requirements, calibrating equipment, mapping temperature distribution, accounting for product load, determining dwell time, performing regular re-qualification, leveraging data analysis, and partnering with experts — you can ensure that your thermal validation process is both effective and efficient.
How Incepbio Can Help You
At Incepbio, we specialize in providing comprehensive validation services for pharmaceutical and medical device companies. Our team of experts can guide you through every step of the thermal validation process, from designing your validation protocol to executing the tests and analyzing the data. With our advanced technology and expertise, we ensure that your systems are compliant with regulatory standards and optimized for peak performance. Reach out to Incepbio today to achieve the best thermal validation results for your operations!