Introduction
Welcome to our blog on equipment validation in the pharmaceutical industry! If you’re a founder, manager, or an employee in a pharmaceutical manufacturing company, this post is for you.
Equipment validation is a critical part of ensuring that your products meet quality and safety standards. In this blog, we’ll answer ten burning questions about equipment validation. Our goal is to help you understand the ins and outs of this important process. So, let’s dive in!
What is Equipment Validation in the Pharmaceutical Industry?
Equipment validation in the pharmaceutical industry means checking and documenting that the equipment used in manufacturing works correctly and consistently. This is essential for producing safe and effective medicines. Regulatory bodies like the FDA require equipment validation to ensure product quality and patient safety.
Why is Equipment Validation Crucial in the Pharmaceutical Industry?
Ensuring Product Quality and Safety:
Equipment validation ensures that every piece of equipment used in the manufacturing process performs as expected, producing high-quality products.
For example, if a machine filling capsules doesn’t work correctly, some capsules might have too much or too little medicine. This can be dangerous for patients.
- Compliance with Regulatory Standards: Regulatory bodies such as the FDA and EMA have strict guidelines for equipment validation. Following these guidelines helps companies avoid legal issues and product recalls.
For instance, the FDA’s Code of Federal Regulations (CFR) Title 21, Part 820, deals with quality system regulations, including equipment validation.
- Minimizing Risks and Avoiding Costly Errors: Validated equipment reduces the risk of errors in the production process. This means fewer product recalls and less waste, saving money in the long run.
For example, a validated sterilizer ensures that all products are sterilized correctly, preventing contamination.
How is Equipment Validation Conducted in the Pharma Industry?
Equipment validation is a systematic process that includes several steps to ensure the equipment works as intended. The main steps are Design Qualification (DQ), Installation Qualification (IQ), Operational Qualification (OQ), and Performance Qualification (PQ).
What are the Key Phases of Equipment Validation?
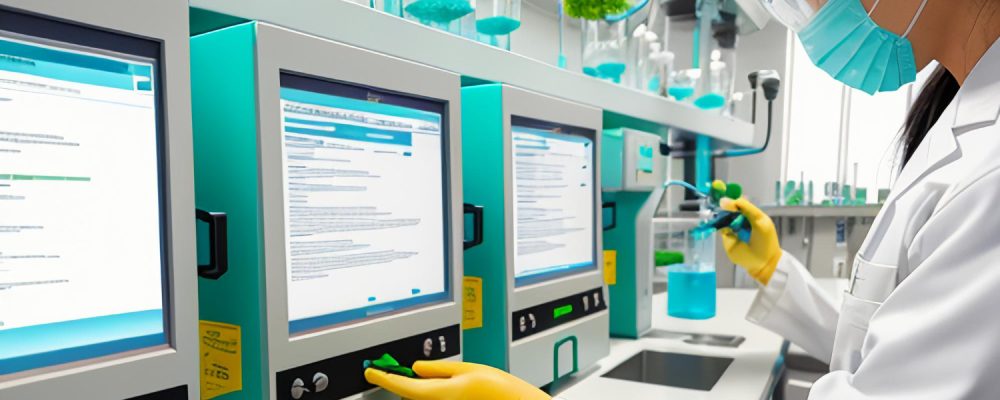
- Design Qualification (DQ): DQ verifies that the design of the equipment meets all the required specifications and regulatory standards before it is installed. It ensures that the equipment is designed correctly to perform its intended function in the pharmaceutical manufacturing process.
- Installation Qualification (IQ): IQ verifies that the equipment is installed correctly and according to the manufacturer’s specifications. This includes checking if all parts are in place and if the installation environment meets the necessary conditions.
- Operational Qualification (OQ): OQ tests the equipment to ensure it operates within the specified limits. For example, it checks if a mixer blends ingredients uniformly at different speeds.
- Performance Qualification (PQ): PQ ensures the equipment performs consistently during regular operation. For instance, it checks if a tablet press produces tablets of the correct weight and hardness over a full production run.
When Should Equipment Validation be Performed in the Pharmaceutical Industry?
- Initial Validation During Equipment Installation: Equipment should be validated when it is first installed. This ensures it works correctly before it is used in production.
- Periodic Re-Validation Schedules: Equipment should be re-validated at regular intervals. This ensures it continues to perform correctly over time. The frequency of re-validation depends on the equipment and its use.
- Situations Requiring Re-Validation: Equipment should be re-validated after repairs, modifications, or relocation. For example, if a filling machine is moved to a new location, it should be re-validated to ensure it still works correctly.
What are the Triggers for Re-Validation of Equipment?
- Equipment Modifications and Upgrades: If equipment is modified or upgraded, it should be re-validated. For example, if a new software update is installed on a machine, re-validation ensures it still performs as expected.
- Changes in Production Processes: If the production process changes, the equipment should be re-validated to ensure it works correctly with the new process. For instance, changing the type of material used in production may affect equipment performance.
- Regulatory Updates and Changes in Guidelines: If regulatory guidelines change, equipment may need to be re-validated to comply with the new standards. Staying updated with regulatory changes is crucial for maintaining compliance.
Who is Responsible for Equipment Validation in the Pharmaceutical Industry?
Equipment validation involves multiple stakeholders, including validation engineers, quality assurance teams, and production managers. Each has specific roles and responsibilities to ensure successful validation.
How to Assemble an Effective Validation Team?
- Key Roles and Expertise Required: A validation team should include experts in equipment operation, quality assurance, and regulatory compliance. For example, a validation engineer designs and executes validation protocols, while a quality assurance specialist ensures compliance with guidelines.
- Training and Qualifications of Validation Personnel: Validation personnel should have the necessary training and qualifications. This includes understanding validation principles, regulatory requirements, and specific equipment functions.
What are the Common Challenges in Equipment Validation and How to Overcome Them?
- Common Challenges Faced During Equipment Validation: Some common challenges include lack of resources, inadequate documentation, and insufficient training. These challenges can lead to delays and non-compliance.
- Best Practices and Strategies to Address These Challenges: To overcome these challenges, companies should allocate sufficient resources, maintain comprehensive documentation, and ensure continuous training for validation personnel. For example, using electronic documentation systems can improve record-keeping and accessibility.
Why Do Equipment Validation Projects Fail?
- Common Pitfalls and Mistakes: Equipment validation projects often fail due to poor planning, lack of clear protocols, and inadequate testing. For instance, skipping steps in the validation process can lead to incomplete validation.
- Case Studies of Failed Validation Projects and Lessons Learned: A case study of a failed validation project might involve a company that rushed through the validation process, resulting in equipment malfunctions and a product recall. The lesson learned is the importance of thorough and systematic validation.
How to Ensure Continuous Compliance in Equipment Validation?
- Ongoing Monitoring and Maintenance: Continuous monitoring and maintenance are essential for ensuring equipment remains validated. This includes regular inspections, calibrations, and performance checks.
- Importance of Documentation and Record-Keeping: Maintaining detailed records of validation activities is crucial for demonstrating compliance. Documentation should include validation protocols, test results, and maintenance logs.
What are the Best Practices for Maintaining Validation Records?
- Documentation Requirements and Standards: Validation records should meet regulatory requirements and standards. This includes following guidelines like the FDA’s CFR Title 21, Part 11, which deals with electronic records and signatures.
- Tools and Technologies for Efficient Record-Keeping: Using electronic record-keeping systems can improve efficiency and accuracy. These systems allow for easy access, updates, and audits of validation records.
What are the Latest Trends and Innovations in Equipment Validation?
- Technological Advancements and Their Impact on Validation Processes: Advances in technology are transforming equipment validation. For example, automated validation systems reduce manual effort and improve accuracy.
- Future Trends in Equipment Validation: Future trends in equipment validation include the use of artificial intelligence and machine learning to predict equipment performance and identify potential issues.
How is Digitalization Transforming Equipment Validation in the Pharmaceutical Industry?
- Role of Digital Tools and Software in Validation: Digital tools and software streamline the validation process. For example, validation management software can automate protocol creation, testing, and reporting.
- Benefits of Adopting Digital Validation Solutions: Digital validation solutions offer several benefits, including improved efficiency, reduced errors, and easier compliance with regulatory requirements. For example, digital signatures eliminate the need for paper records and facilitate audits.
How Can Incepbio Help in Equipment Validation?
Incepbio is a trusted partner in the pharmaceutical industry, offering comprehensive equipment validation services. Our team of experts ensures that your equipment meets regulatory standards and operates efficiently. We provide:
- Comprehensive Validation Services: Incepbio offers complete validation services, including IQ, OQ, and PQ. Our team ensures your equipment is validated according to the latest regulatory guidelines.
- Expert Team: Our validation team consists of highly trained professionals with extensive experience in the pharmaceutical industry. We provide training and support to ensure your team is equipped to maintain validated equipment.
- Advanced Tools and Technologies: Incepbio uses the latest tools and technologies to streamline the validation process. Our digital validation solutions improve efficiency and accuracy, ensuring continuous compliance.
- Ongoing Support and Maintenance: We offer ongoing support and maintenance services to ensure your equipment remains validated. Our team provides regular inspections, calibrations, and performance checks to keep your equipment in top condition.
For more information on how Incepbio can help with your equipment validation needs, visit our website at Incepbio.com.
Parting Thoughts
Equipment validation is a critical aspect of pharmaceutical manufacturing, ensuring product quality, safety, and compliance with regulatory standards. By following best practices and staying updated with the latest trends and technologies, companies can overcome validation challenges and maintain continuous compliance.
Partnering with experts like Incepbio can help streamline the validation process and ensure success. Thank you for reading, and we hope this blog has provided valuable insights into equipment validation in the pharmaceutical industry.
Additional Resources
Pharmaceutical Compliance Resources
Contact us at Incepbio.com for expert consultation and support.