Temperature uniformity is a critical component of thermal validation, particularly in industries like pharmaceuticals, biotechnology, and food production. During thermal validation, it is essential to ensure that the temperature is consistent throughout the validated space or system. Variations in temperature can lead to product degradation, loss of efficacy, and non-compliance with regulatory standards. In this blog, we will discuss the five key metrics you should monitor to ensure temperature uniformity during thermal validation.
1. Spatial Temperature Variation
Spatial temperature variation refers to the differences in temperature readings across different locations within a controlled environment. In any thermal validation process, it’s crucial to measure temperature at various points within the space, including corners, shelves, and near vents, to ensure uniform distribution.
Why It’s Important:
Temperature inconsistencies across different locations can lead to localized overheating or cooling, which can affect product integrity, especially for temperature-sensitive materials.
How to Monitor It:
- Place temperature sensors in representative locations throughout the environment, including areas that are prone to temperature fluctuations (e.g., near doors, windows, or air vents).
- Use multiple sensors to cover all zones and account for potential hot or cold spots.
- Analyze the data to identify significant deviations and take corrective action if needed.
Read More: 8 Secrets You Must Know for Best Thermal Validation Results
2. Temperature Gradient
A temperature gradient measures the rate of temperature change between different areas of the system or environment. During thermal validation, you need to evaluate how temperature changes across different zones and whether it remains consistent over time.
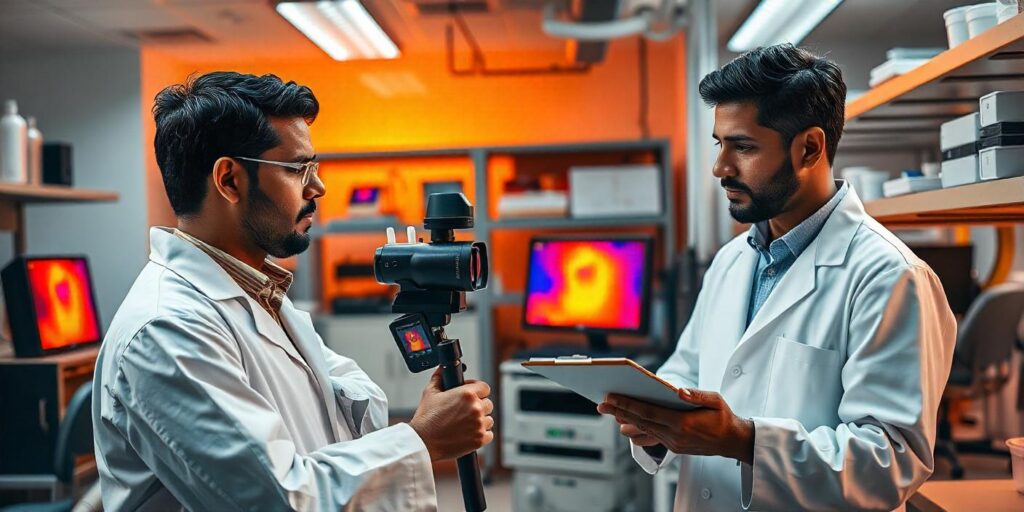
Why It’s Important:
A high temperature gradient could indicate poor insulation, inadequate airflow, or faulty equipment, which could lead to uneven temperature distribution, ultimately compromising product safety.
How to Monitor It:
- Track temperature data over a period of time to see how it fluctuates from one location to another.
- Use a network of data loggers that record real-time temperature data in multiple zones.
- Compare the temperature difference between various points and ensure it is within acceptable limits as specified in regulatory guidelines.
Read More: 10 Burning Questions on CQV
3. Maximum and Minimum Temperature
The maximum and minimum temperature readings are essential metrics that help assess whether the temperature is staying within the defined range. These extreme values are critical in identifying potential outliers and ensuring that the temperature conditions do not exceed the acceptable thresholds for product safety.
Why It’s Important:
If the temperature fluctuates beyond the allowed limits, even for short periods, it can compromise the integrity of the product, especially in temperature-sensitive materials like vaccines, biologics, or food items.
How to Monitor It:
- Set alarms for the maximum and minimum temperature limits based on product requirements and regulatory guidelines.
- Regularly check the maximum and minimum temperature for each zone during the validation process to ensure no critical outliers.
- Perform post-validation analysis to determine if any excursions have occurred and whether corrective actions are necessary.
Read More: Thermal Validation-5 New Cutting-Edge Technologies
4. Average Temperature
The average temperature is an essential metric to track the overall temperature of the system. While maximum and minimum temperatures provide insights into fluctuations, the average temperature gives a clear indication of the general environment’s stability.
Why It’s Important:
Maintaining a consistent average temperature is crucial for ensuring that all products within the space are kept within the acceptable temperature range.
How to Monitor It:
- Monitor the average temperature over the entire validation period to ensure that it aligns with the desired set point.
- Evaluate how the average temperature compares to the target temperature range for your products.
- Ensure that the average temperature stays within the acceptable range and doesn’t show significant deviation over time.
5. Temperature Recovery Time
Temperature recovery time is the amount of time it takes for the system to return to the desired temperature after a disturbance (such as door opening, equipment malfunction, or power failure). It’s essential to understand how quickly and effectively the system can return to the set temperature to maintain uniform conditions.
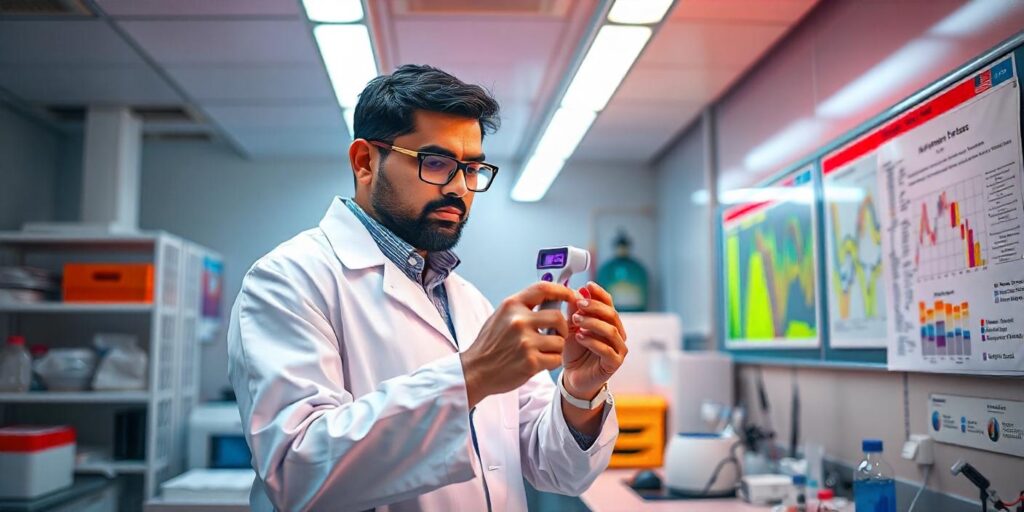
Why It’s Important:
Long recovery times can lead to prolonged temperature excursions, which may have adverse effects on sensitive products. A system with a fast recovery time helps ensure that temperature variations are minimized and controlled.
How to Monitor It:
- Simulate disruptions, such as opening doors or removing a product from the space, to observe how long it takes for the system to return to the desired temperature.
- Use temperature loggers that track both real-time temperature changes and recovery times.
- Analyze the recovery time data to determine whether it meets the system’s specifications and operational requirements.
Read More: Thermal Validation: 8 Critical Regulatory Standards You Must Know
Conclusion
Monitoring temperature uniformity is a crucial part of thermal validation, and the five metrics discussed—spatial temperature variation, temperature gradient, maximum and minimum temperature, average temperature, and temperature recovery time—play a significant role in ensuring that products are maintained under optimal conditions. By monitoring these key metrics, you can identify potential issues, optimize the validation process, and ensure compliance with regulatory requirements.
How Incepbio Can Help You
At Incepbio, we provide expert solutions for monitoring temperature uniformity during thermal validation. Our team helps you design and implement customized temperature monitoring strategies, ensuring that your systems meet the highest industry standards. With advanced equipment, comprehensive data analysis, and regulatory guidance, we ensure your thermal validation process is efficient and effective, protecting the integrity of your products.
For more information or assistance with your thermal validation needs, contact us today!
Authors
-
-
Arjun Jha has over 8 years of experience in tech startups, business strategy, and digital and traditional marketing. He’s helped many startups grow by using creative strategies and a deep understanding of the market. Outside of work, Arjun enjoys reading about business, philosophy, psychology, and spirituality, which inspires his unique approach to problem-solving and growth.
View all posts -
An experienced SEO professional, Adithya is someone fascinated by the art of content creation. He has published over 700 articles under his name. Additionally, he has worked for companies like TCS, Essentially Sports, and holds expertise in the field of digital marketing
View all posts