When it comes to CQV (Commissioning, Qualification, and Validation), there’s a lot of information—and misinformation—out there. If you’re in pharmaceutical or medical device manufacturing, you know how critical the process is for compliance and quality control. But are certain myths making it harder than it needs to be? Today, we’ll debunk eight of the biggest myths about commissioning, qualification, and validation that could be hindering your team’s success.
Let’s clarify these myths so you can make better-informed decisions in your processes and achieve seamless regulatory compliance.
1. Myth: CQV is Only Necessary for New Equipment
Many think CQV only applies to new equipment or systems, but that’s a misconception. Validation is essential any time there’s a change that could impact product quality, whether it’s a process update, facility expansion, or equipment modification.
Reality: Validation applies to all equipment and systems that could affect product safety or quality, even when making minor adjustments. For example, if a pharmaceutical facility upgrades its HVAC system, revalidating environmental controls ensures compliance and operational integrity. Routine assessments are crucial to maintaining a validated state.
2. Myth: CQV is a One-Time Process
The idea that CQV is a “set it and forget it” process is another common myth. In reality, validation is a continuous process that needs to adapt to regulatory updates, process changes, and technological advancements.
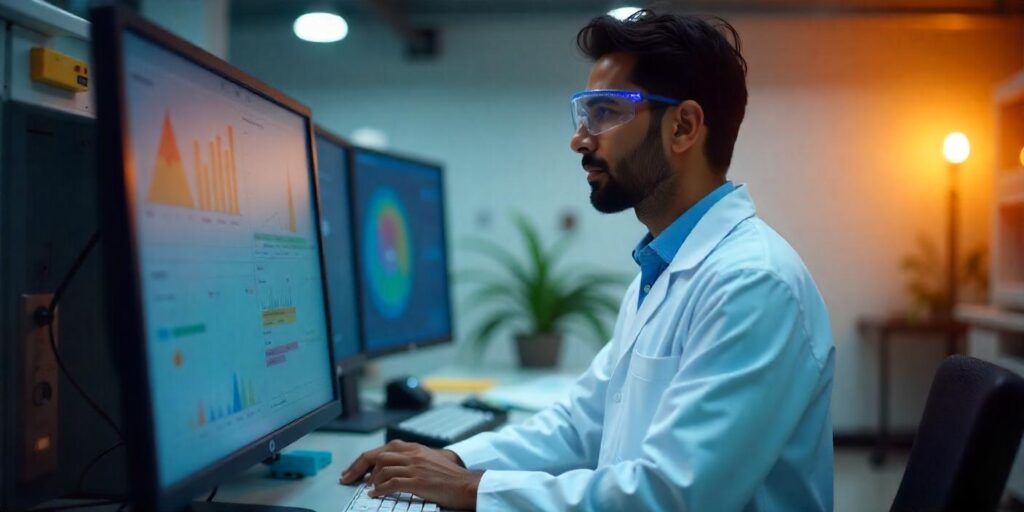
Reality: CQV requires regular monitoring and periodic requalification to maintain compliance. For instance, the FDA and EMA frequently update guidelines, meaning that initial qualifications may need to be revisited. Treating it as a living process keeps your facility in line with regulatory standards and helps you stay proactive rather than reactive.
3. Myth: Only Large Companies Need it
Some believe that only large pharmaceutical and medical device companies need CQV due to the resources required. But in today’s regulatory environment, all companies—big or small—must ensure that their processes are thoroughly validated.
Reality: CQV is essential for companies of all sizes to meet regulatory standards, which protect patient safety and product efficacy. Small to mid-sized companies can use strategic planning and scaled approaches to meet requirements without overwhelming their resources. Whether you’re a startup or an established player, CQV supports compliance and market credibility.
4. Myth: It is Just a Checklist
Viewing validation as a rigid checklist to complete leads to a shallow approach that can miss critical issues. This myth results in hurried processes focused on ticking boxes rather than ensuring genuine quality and compliance.
Reality: CQV is a structured but flexible approach, meant to adapt to specific facility needs. Successful CQV integrates risk assessment, process understanding, and ongoing monitoring. Instead of a checklist, think of it as a comprehensive framework that combines planning, testing, and validation tailored to your facility’s unique operations.
Read More: 10 Practical Tips for Reliable CQV Results
5. Myth: Digital Data Integrity Isn’t a Big Concern in CQV
Many manufacturers assume that data integrity is a minor detail in CQV, but that assumption can lead to serious compliance risks. Without reliable data, there’s no way to prove the consistency of your processes.
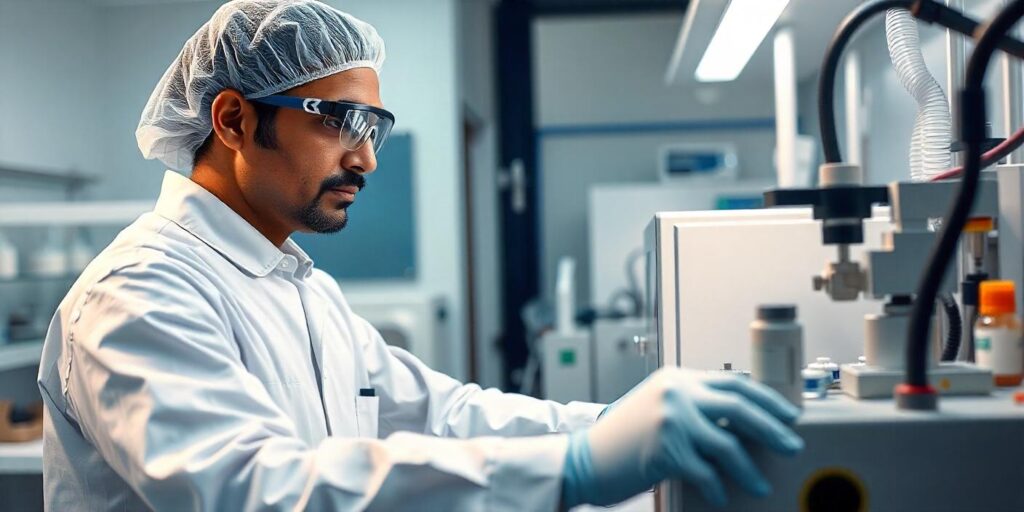
Reality: Data integrity is fundamental in the process, especially with automated systems. Regulatory bodies, including the FDA, require accurate, traceable data to validate processes. Investing in software with audit trails and access controls can help you maintain data integrity and compliance. Failing to address data integrity risks can lead to regulatory scrutiny and jeopardize your product’s approval.
6. Myth: It is Primarily About Equipment and Facilities
Many assume CQV focuses solely on physical assets like equipment and facilities. But validation actually encompasses everything that affects quality, including software systems, processes, and even personnel training.
Reality: CQV extends to all areas impacting product quality, including training for employees involved in critical processes. If your team lacks updated training on new protocols or equipment, they could unknowingly impact product quality. Comprehensive strategies factor in process, personnel, and system qualifications to ensure end-to-end quality.
7. Myth: Outsourcing CQV is an Unnecessary Expense
Many companies believe CQV should always be handled in-house to save money, but outsourcing commissioning, qualification, and validation can provide significant benefits, particularly if you’re facing resource constraints or need specialized expertise.
Reality: Partnering with a specialized CQV service can bring in expertise, speed up project timelines, and improve compliance. For example, Incepbio provides bioburden testing and other critical validation services. With their support, companies can ensure high standards without overextending their in-house resources. Outsourcing key aspects of the validation process can actually be a cost-effective solution that provides quality and efficiency.
8. Myth: It is Just a Regulatory Requirement, Not a Business Advantage
Some professionals view CQV as merely a regulatory requirement that consumes resources and time. This perception can diminish the value it brings to a business.
Reality: CQV is not just about compliance; it can significantly enhance product quality and operational efficiency. A robust validation process can lead to better product consistency, fewer recalls, and enhanced customer trust. By ensuring that every product meets strict quality standards, companies can reduce costs associated with non-compliance and maintain a strong market reputation.
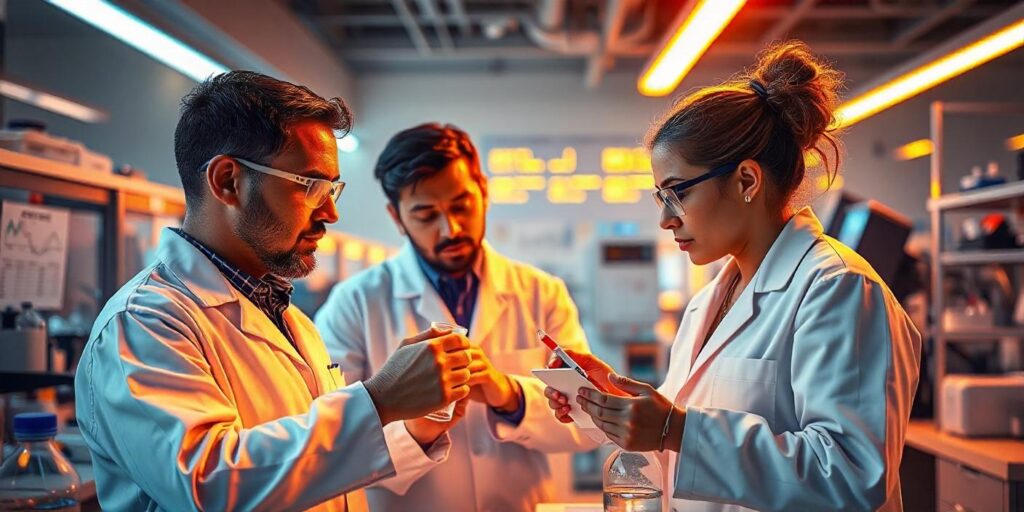
For instance, a pharmaceutical company that implements rigorous CQV practices can experience faster approval times for new drugs, leading to a competitive advantage in the market. This proactive approach can translate into long-term profitability and customer loyalty.
How Incepbio Can Assist with Your CQV Needs
Incepbio is dedicated to supporting your CQV efforts with expert services. Whether you’re upgrading equipment or validating new processes, our team at incepbio.com offers comprehensive solutions to help ensure you meet compliance and quality standards.
Read More: 8 Common Mistakes to Avoid During Commissioning, Qualification, and Validation
Conclusion: Avoid major pitfalls by Recognizing These Myths
Misunderstanding the CQV process can lead to setbacks in compliance and quality, but by recognizing these myths, you’re already taking the first step toward stronger validation practices. Whether it’s understanding that validation isn’t just for large companies or realizing the importance of data integrity, each myth clarified here helps set a clear path for your validation journey.
By addressing these myths, you can approach CQV as a continuous, adaptable process that supports long-term compliance and quality control in your facility. Embracing the process not only safeguards your operations but can also provide a significant business advantage, ultimately leading to enhanced product quality and customer satisfaction.
Authors
-
Shubhankar is a pharmaceutical professional with over 10 + years of experience in Drug Substance (Upstream), Aseptic Batch Manufacturing (Drug Product), Process Validation, and CQV (Commissioning, Qualification, and Validation). He is skilled in managing the qualification and implementation of protocols for URS, DQ, FAT, SAT, IQ, OQ, and PQ for new equipment. Holds sounds knowledge of CSV (Computer System Validation) in compliance with 21 CFR 210/211, 21 CFR Part 11, and European regulations. Shubhankar is experienced in creating cGMP-oriented documentation, including SOPs, BPRs, Calibration Records, and deviation investigations. Expertise in overseeing various validation activities, such as HVAC, Utility, and Process Equipment Validation.
View all posts -
An experienced SEO professional, Adithya is someone fascinated by the art of content creation. He has published over 700 articles under his name. Additionally, he has worked for companies like TCS, Essentially Sports, and holds expertise in the field of digital marketing
View all posts -
Arjun Jha has over 8 years of experience in tech startups, business strategy, and digital and traditional marketing. He’s helped many startups grow by using creative strategies and a deep understanding of the market. Outside of work, Arjun enjoys reading about business, philosophy, psychology, and spirituality, which inspires his unique approach to problem-solving and growth.
View all posts