Ensuring your CQV compliance is secure might feel like navigating a maze. It’s no secret that pharmaceutical and medical device companies face constant pressure to meet high standards of quality and validation. However, the real threat to your CQV compliance may not always lie in procedures or technology—it can start with mindset. In this blog, we’ll dive into five common mindsets that can lead to CQV compliance risks and show you how adjusting these mentalities can safeguard your organization from costly mistakes.
What Are the Common Mindsets That Endanger CQV Compliance?
Our attitudes shape how we approach tasks, and when it comes to CQV compliance, even small shifts in mindset can make a big difference. Let’s look at five mindsets that can subtly but significantly put CQV compliance at risk.
1. “It’s Just a One-Time Issue” Mindset Can Undermine CQV Compliance
A common but dangerous mentality in CQV compliance is brushing off errors as “one-time” incidents. Think about it: how often has a minor deviation gone unaddressed simply because it “only happened once”? This mindset can lead to serious compliance gaps over time.
- Why small issues become big problems: When small issues are overlooked, they tend to recur. Even minor oversights can eventually cause deviations significant enough to trigger regulatory audits or product recalls.
- Case in point: In a study by the FDA, over 40% of warning letters issued to manufacturers stemmed from cumulative minor infractions that were initially deemed “one-offs” but escalated due to inaction.
Adopt a habit of investigating even minor issues. Documentation and corrective actions should be applied consistently, ensuring that small deviations don’t snowball into compliance threats.
Read More: 6 Things to Know When You Are Choosing Your CQV Compliance Partner
2. “We’ve Always Done It This Way” Mindset Put CQV Compliance at Risk
In CQV, processes often come with a long history of “doing things the way they’ve always been done.” But what happens when regulatory standards evolve? Sticking to outdated processes can prevent teams from keeping up with new requirements and industry standards.
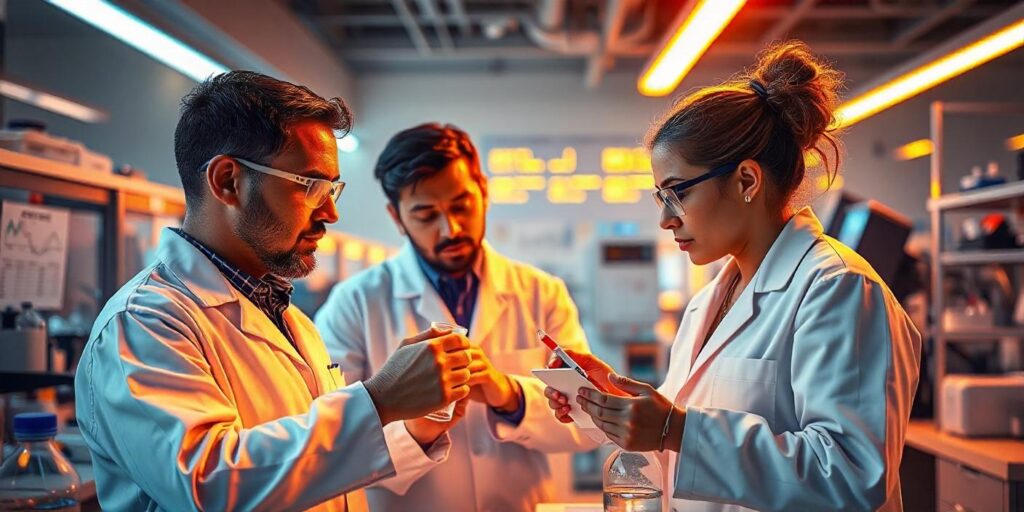
- The risk of relying on tradition: Regulatory bodies such as the FDA or EMA regularly update their guidelines. Failure to stay current with these changes can leave your company vulnerable to compliance risks.
- Example: Imagine a manufacturing process based on legacy equipment, which may not meet updated sterility standards. Relying solely on outdated methods may eventually lead to non-compliance if modern standards are not integrated.
Encourage regular audits of processes and be open to change. Incepbio.com, for instance, regularly helps clients update CQV processes to align with current standards, helping them avoid the pitfalls of an outdated mindset.
3. “Compliance Is Just a Checklist” Attitude
Viewing CQV compliance as just another checkbox to tick can lead to a surface-level approach that misses the bigger picture. When teams see compliance as a task to complete rather than a culture to cultivate, it’s easy to overlook critical safety and quality measures.
- Beyond the checklist: Compliance involves not only following guidelines but understanding their purpose. For instance, the purpose of risk assessments in CQV goes beyond paperwork; it’s about identifying potential failures that could impact product quality or patient safety.
- Data to consider: In an analysis of non-compliance cases, the World Health Organization (WHO) found that over 60% were due to neglecting quality details beyond standard procedures.
Educate teams on the “why” behind compliance standards to foster a sense of responsibility beyond checklists. By integrating CQV into the organization’s culture, it becomes a proactive pursuit rather than a routine chore.
4. “Reactive Instead of Proactive” Mindset can Harm CQV Compliance
Another risky mindset is waiting to react to compliance issues rather than proactively seeking to prevent them. When CQV becomes a series of reactive responses, your organization is essentially one step behind potential problems.
- The cost of waiting: Studies by Deloitte suggest that organizations with proactive quality management programs see a 20% reduction in compliance costs compared to those that handle issues reactively.
- Story of impact: Incepbio has assisted clients who previously only addressed compliance after issues arose. By shifting to a proactive approach, these clients reduced non-compliance incidents significantly, ultimately saving on time and resources.
Implement regular training and internal audits to identify and address risks before they escalate. Building a proactive culture not only reduces risk but also boosts efficiency and team confidence.
Read More: 11 Critical Truths About FDA Observations on CQV Compliance That You Need to Know
5. “Minimal Investment” Mindset
When CQV compliance is viewed as a cost to minimize, quality risks increase. The minimal investment mentality often results in cutting corners, limited training, or outdated technology—all of which can eventually backfire.
- The hidden costs of minimal investment: A study by McKinsey & Company found that companies investing adequately in quality measures achieved a 22% lower rate of quality incidents, reducing costs in the long run.
- Example of a missed opportunity: One company Incepbio worked with initially hesitated to upgrade its validation processes due to budget concerns. However, after a minor non-compliance incident led to a significant production halt, they realized that upfront investment in quality is often cheaper than addressing compliance issues later.
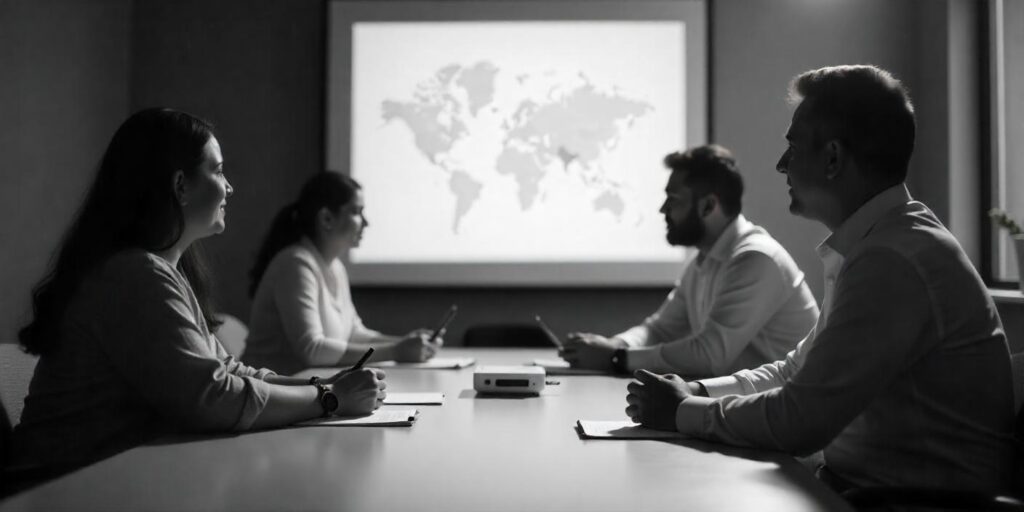
Invest wisely in CQV training, technology, and resources to support robust compliance. Partnering with experts like Incepbio, who work with industrial giants, ensures access to updated validation strategies and practices, enhancing long-term compliance.
Read More: 7 CQV Secrets to Keep Your Equipment Safe in Pharmaceutical Manufacturing
How Can You Cultivate a Compliance-First Mindset for Sustainable CQV Success?
Changing these mindsets requires a shift in organizational culture and leadership. A compliance-first mindset emphasizes consistency, attention to detail, and commitment at every level of the organization.
- Steps to foster a compliance-driven culture:
- Start with leadership—team leaders and executives should model a proactive approach to compliance.
- Conduct regular training sessions that connect compliance guidelines to real-life impact.
- Implement audits as opportunities for learning, not just for correction.
- How Incepbio Can Help: At Incepbio, we specialize in guiding companies towards sustainable CQV compliance. Our clients benefit from customized compliance solutions, continuous training, and up-to-date practices. Visit incepbio.com to learn more about how we can support your CQV needs.
Conclusion
CQV compliance is more than a set of guidelines—it’s a commitment that starts with the right mindset. By shifting away from these five risk-inducing mentalities, your organization can foster a culture of proactive, quality-focused compliance. From seeing compliance as more than just a checklist to understanding the value of investment, each change contributes to a more robust and resilient CQV process.
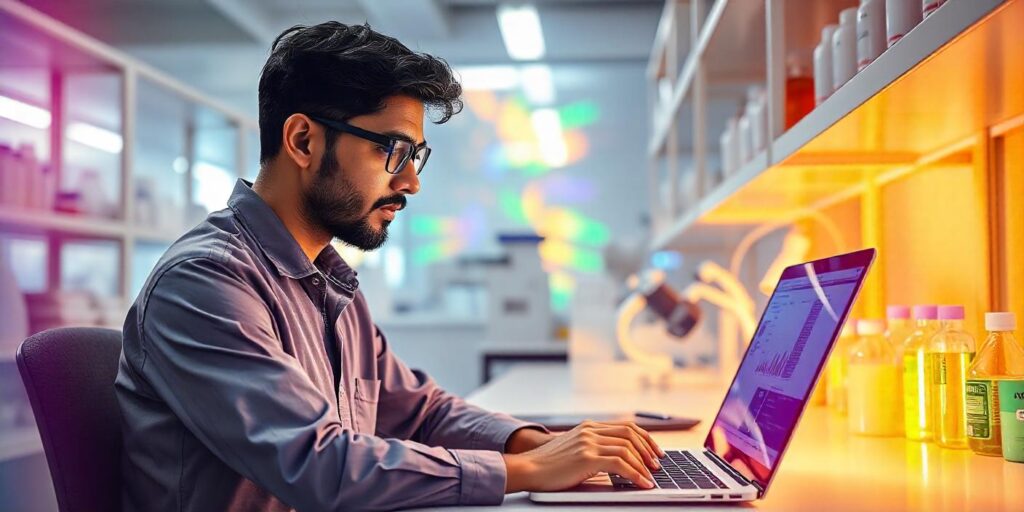
With Incepbio’s expertise, you’re never alone in achieving sustainable CQV compliance.
Authors
-
Shubhankar is a pharmaceutical professional with over 10 + years of experience in Drug Substance (Upstream), Aseptic Batch Manufacturing (Drug Product), Process Validation, and CQV (Commissioning, Qualification, and Validation). He is skilled in managing the qualification and implementation of protocols for URS, DQ, FAT, SAT, IQ, OQ, and PQ for new equipment. Holds sounds knowledge of CSV (Computer System Validation) in compliance with 21 CFR 210/211, 21 CFR Part 11, and European regulations. Shubhankar is experienced in creating cGMP-oriented documentation, including SOPs, BPRs, Calibration Records, and deviation investigations. Expertise in overseeing various validation activities, such as HVAC, Utility, and Process Equipment Validation.
View all posts -
An experienced SEO professional, Adithya is someone fascinated by the art of content creation. He has published over 700 articles under his name. Additionally, he has worked for companies like TCS, Essentially Sports, and holds expertise in the field of digital marketing
View all posts -
Arjun Jha has over 8 years of experience in tech startups, business strategy, and digital and traditional marketing. He’s helped many startups grow by using creative strategies and a deep understanding of the market. Outside of work, Arjun enjoys reading about business, philosophy, psychology, and spirituality, which inspires his unique approach to problem-solving and growth.
View all posts