Thermal validation is a crucial process in industries such as pharmaceuticals, food production, and medical device manufacturing. It ensures that products are subjected to the appropriate temperature conditions during storage, transportation, and manufacturing. Proper thermal validation not only helps in meeting regulatory requirements but also ensures the quality and safety of products. However, there are several aspects of thermal validation that may be misunderstood or overlooked. In this blog, we’ll discuss six key truths you need to know about thermal validation.
1. Thermal Validation Is More Than Just Temperature Monitoring
Many people think thermal validation is simply about monitoring temperature during the production or storage phases. While temperature monitoring is a critical part of the process, thermal validation goes beyond just taking measurements.
Why It Matters: Thermal validation involves analyzing temperature data, assessing the uniformity of temperature distribution, and determining whether temperature variations could affect product quality. It’s about ensuring that the temperature profile meets the specified requirements throughout the entire system or process.
How to Implement:
- Use multiple sensors across different areas to collect temperature data.
- Analyze the data to ensure there are no temperature fluctuations that could compromise the quality or safety of the product.
- Document and adjust processes as needed based on findings from the validation process.
Read More: Thermal Validation: 8 Critical Regulatory Standards You Must Know
2. Thermal Validation Must Consider Both Heat and Cold Conditions
It’s essential to understand that thermal validation applies not just to high-temperature environments, but also to cold conditions. Whether you’re validating a freezer, refrigerator, or autoclave, both ends of the temperature spectrum require attention.
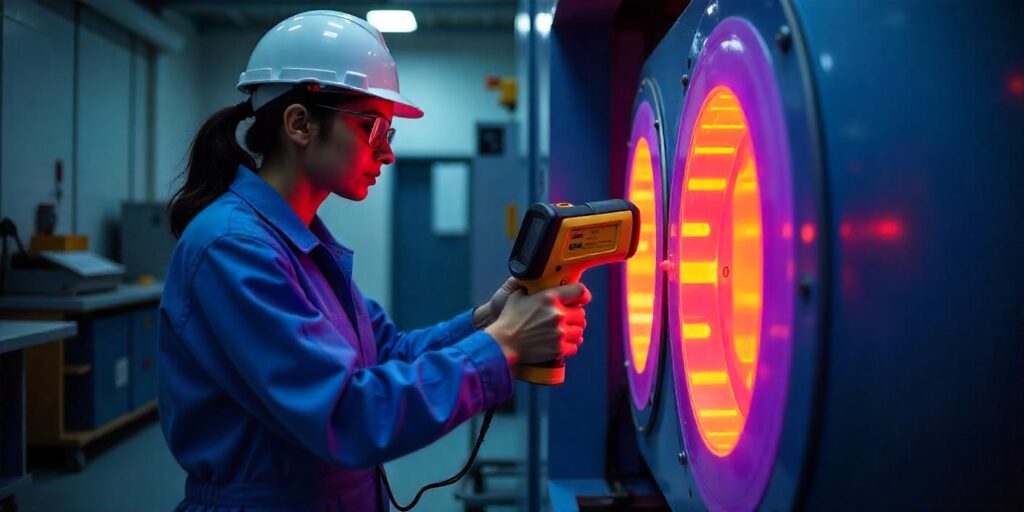
Why It Matters: Temperature fluctuations in both hot and cold environments can lead to compromised product integrity. In the case of pharmaceuticals or food, improper cold storage could result in degradation, while excessive heat could spoil a product or cause instability.
How to Implement:
- Ensure that temperature extremes (high and low) are validated across the relevant range for your product.
- Take into account the entire temperature cycle, from the coldest to the hottest points.
- Perform tests under both standard and extreme temperature conditions to verify the robustness of the temperature control system.
Read More: Top 10 Challenges in Thermal Validation and How to Overcome Them
3. It’s About Consistency, Not Just Meeting a Single Temperature
One of the most common mistakes in thermal validation is focusing solely on achieving a single target temperature. While this is important, what really matters is the consistency of temperature over time and across the entire process.
Why It Matters: Inconsistent temperatures can lead to hotspots or cold spots in storage and processing environments, which can affect product quality, shelf life, or safety. Achieving a stable temperature is just as critical as reaching the desired temperature.
How to Implement:
- Run long-term validation tests to ensure that temperature consistency is maintained throughout the process.
- Evaluate and optimize equipment or systems that cause temperature variations.
- Record temperature data over extended periods to confirm that variations fall within acceptable ranges.
4. Thermal Validation is Crucial for Compliance with Regulatory Standards
Whether you’re in the pharmaceutical, medical device, or food industry, regulatory bodies require strict compliance with temperature control during production and storage. Thermal validation is not optional—it is a fundamental requirement for compliance.
Why It Matters: Regulatory bodies such as the FDA (U.S. Food and Drug Administration), EMA (European Medicines Agency), and others mandate strict guidelines for temperature control to ensure product safety. Failure to comply can lead to costly fines, product recalls, or even the suspension of business operations.
How to Implement:
- Understand and adhere to the regulations relevant to your industry, including guidelines from the FDA, ISO, or WHO.
- Keep thorough records of thermal validation processes, including temperature data, sensor calibration, and corrective actions taken.
- Schedule regular revalidation as required by regulatory standards.
5. Accurate Calibration of Equipment Is Essential
For effective thermal validation, the equipment used to measure and control temperature must be properly calibrated. Without accurate calibration, you can’t rely on the results, and your validation process could be compromised.
Why It Matters: Improperly calibrated sensors or equipment can result in incorrect temperature measurements, leading to inaccurate conclusions about your validation process. This can have serious implications for product quality and regulatory compliance.
How to Implement:
- Regularly calibrate temperature sensors and monitoring devices to ensure they are working accurately.
- Use equipment that meets industry standards and ensure calibration is done by certified professionals.
- Keep calibration records and certifications for future audits.
Read More: Thermal Validation: 5 New Cutting-Edge Technologies
6. Thermal Validation Requires Ongoing Monitoring and Revalidation
Thermal validation is not a one-time process. It’s an ongoing responsibility to ensure that systems continue to operate within the required temperature parameters. Factors such as equipment wear, changes in operational procedures, or external environmental changes can affect temperature consistency.
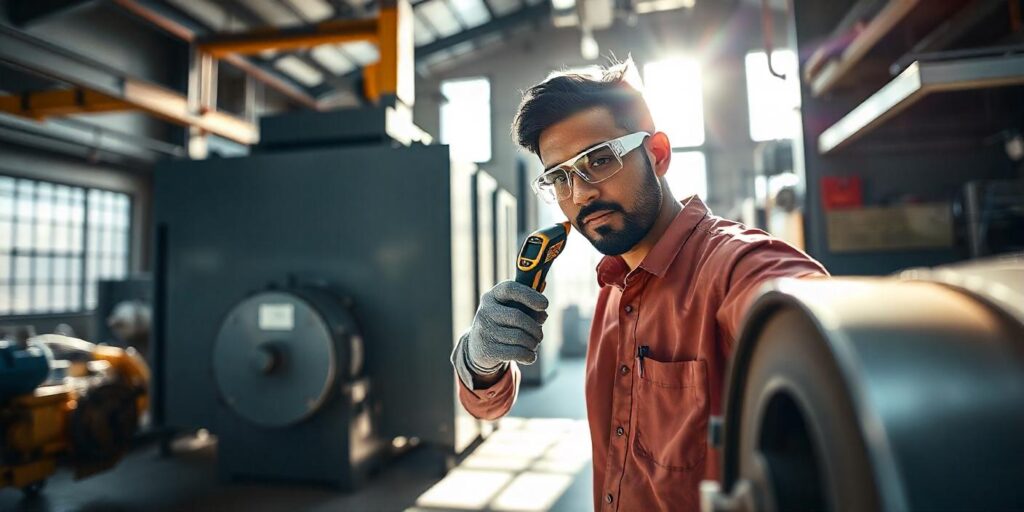
Why It Matters: Continuous monitoring and revalidation ensure that temperature conditions are maintained throughout the lifecycle of your products. This proactive approach helps prevent potential issues before they compromise the product’s quality or safety.
How to Implement:
- Implement continuous temperature monitoring systems that provide real-time data and alerts when temperatures fall outside acceptable ranges.
- Schedule periodic revalidation to check whether the systems are still compliant with your standards and regulations.
- Regularly review your equipment and processes to identify areas where improvements can be made to optimize temperature control.
How Incepbio Can Help with Thermal Validation
Incepbio provides comprehensive thermal validation services that ensure your systems are compliant with industry standards and regulations. Our services help you achieve optimal temperature control and maintain product quality throughout the manufacturing, storage, and transportation processes. Here’s how we can assist:
- Expert Consultation: Incepbio offers expert advice on thermal validation, helping you understand regulatory requirements and best practices for your specific industry.
- Customized Validation Plans: We develop tailored validation plans to meet your unique needs, whether you’re dealing with high-temperature autoclaves or low-temperature storage environments.
- Advanced Monitoring Systems: We use state-of-the-art monitoring equipment to track temperature conditions accurately, ensuring consistency and compliance throughout your processes.
- Thorough Documentation: We provide complete documentation of the thermal validation process, which can be used for audits, regulatory inspections, and internal records.
- Ongoing Support and Revalidation: Incepbio offers ongoing support and periodic revalidation to ensure your thermal systems continue to operate within the required temperature ranges over time.
Read More: 8 Secrets You Must Know for Best Thermal Validation Results
Conclusion
Thermal validation is a critical process for ensuring product quality, safety, and regulatory compliance. By understanding these six truths—going beyond basic temperature monitoring, considering both heat and cold conditions, focusing on consistency, meeting regulatory standards, calibrating equipment, and conducting ongoing monitoring—you can optimize your thermal validation efforts. Partnering with Incepbio ensures that your validation process is thorough, efficient, and compliant, helping you maintain the highest standards in temperature control and product safety.
Authors
-
-
An experienced SEO professional, Adithya is someone fascinated by the art of content creation. He has published over 700 articles under his name. Additionally, he has worked for companies like TCS, Essentially Sports, and holds expertise in the field of digital marketing
View all posts -
Arjun Jha has over 8 years of experience in tech startups, business strategy, and digital and traditional marketing. He’s helped many startups grow by using creative strategies and a deep understanding of the market. Outside of work, Arjun enjoys reading about business, philosophy, psychology, and spirituality, which inspires his unique approach to problem-solving and growth.
View all posts