Imagine setting up a complex pharmaceutical manufacturing process only to discover, a few months in, that something critical was overlooked. Equipment malfunctions, processes fail, and compliance is jeopardized. Sound familiar? For anyone involved in pharmaceutical and medical device manufacturing, ensuring product quality and regulatory compliance is non-negotiable. That’s where Commissioning, Qualification, and Validation (CQV) comes into play.
In this blog, we’re diving into six truths about commissioning, qualification, and validation that will clarify misconceptions and reveal how this process does much more than ticking regulatory boxes. Let’s uncover why the process is a game-changer for efficiency, quality, and compliance—and how it’s the foundation for smooth, risk-free operations in your business.
What Is CQV and Why Does It Matter?
CQV is the foundation of safety and consistency in highly regulated industries like pharmaceuticals. It involves a series of steps to ensure that equipment, systems, and processes function precisely as intended. Hence, it isn’t exactly a “one-and-done” task; it’s a continuous commitment to quality, from equipment setup to final product release.
Read More: 7 CQV Secrets to Keep Your Equipment Safe in Pharmaceutical Manufacturing
Ensuring the right approach can prevent costly errors, avoid compliance issues, and set up production for success. So, what are the truths about CQV that you need to know? Let’s dive in!
Truth #1 – CQV Goes Beyond Initial Equipment Setup
It’s tempting to think that once equipment is up and running, there isn’t further need for commissioning, qualification, and validation. But it doesn’t end after installation—it’s an ongoing responsibility. Why? Because equipment, processes, and regulatory expectations are constantly evolving.
Imagine a situation where new guidelines emerge after a system is up and running. Without continual validation, there’s a risk of non-compliance. Keeping up with CQV ensures that your processes meet the latest standards, adapt to process changes, and operate at peak efficiency.
Example:
A major pharmaceutical company invested heavily in an initial CQV process but skipped regular re-validation. The oversight led to unexpected regulatory non-compliance, product quality issues, and loss of market trust. Lesson learned: It is infact a continuous journey, not a final destination.
Truth #2 – It Can Optimize Operational Efficiency
CQV might sound like an extra step, but it’s a smart investment in operational efficiency. A well-executed strategy reduces downtime, identifies potential issues early, and ultimately streamlines production.
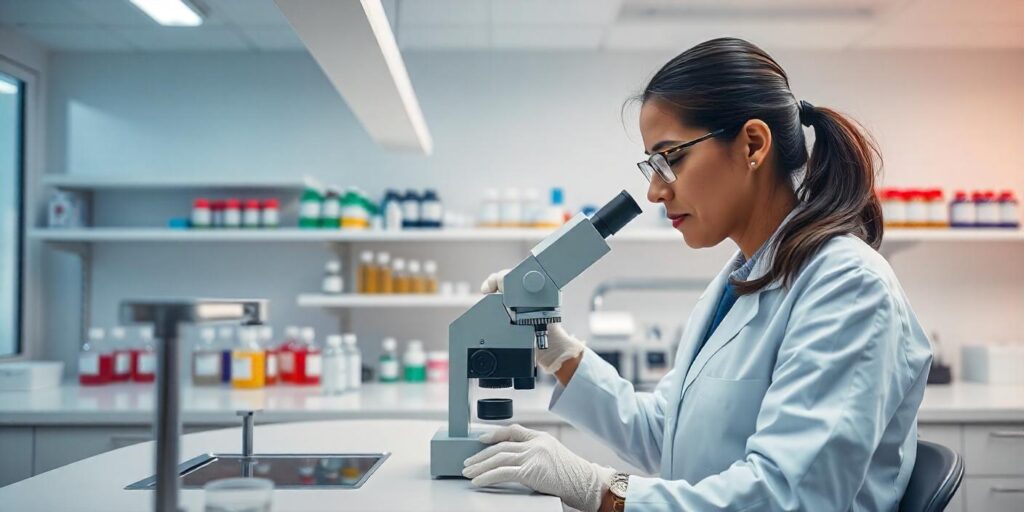
By catching issues upfront, CQV helps you avoid costly surprises that disrupt production. Consider it preventive maintenance on a larger scale—avoiding the high costs of emergency repairs and product recalls.
Data Point:
According to industry research, pharmaceutical companies implementing a comprehensive validation process reduce operational disruptions by up to 30% annually. This not only keeps production running smoothly but also cuts down on unexpected costs.
Truth #3 – Documentation Is Not Just a Regulatory Requirement but a Strategic Asset
Documenting the CQV process isn’t just about satisfying auditors. Clear, organized documentation provides a roadmap for quality assurance, serving as a reference point for future training and process improvement.
Proper documentation allows teams to understand past decisions, identify what’s working, and catch issues before they become problems. In the event of an audit, this documentation is invaluable. Think of it as the blueprint that ensures compliance, consistency, and accountability.
Example:
When a medical device company faced an unexpected FDA audit, their well-maintained CQV documentation saved the day. The auditors were impressed by the organization’s transparency and preparedness, which led to a smooth, issue-free audit.
Truth #4 – Not All Equipment Requires the Same Level of Validation
Not every piece of equipment requires the same CQV rigor. A risk-based approach to CQV helps prioritize efforts based on equipment’s role and potential impact on product quality.
For instance, critical equipment directly affecting the product might need extensive validation, while ancillary equipment requires minimal validation. By tailoring the validation process to the equipment’s function and risk level, you can optimize both time and resources without compromising quality.
Read More: 8 Common Mistakes to Avoid During Commissioning, Qualification, and Validation
Truth #5 – It Requires Cross-Functional Collaboration
CQV is not a solo endeavor—it’s a team effort involving quality assurance, engineering, operations, and sometimes even external consultants. Collaboration ensures a holistic approach, where every expert contributes to achieving compliance and performance goals.
When multiple teams are aligned on their validation goals, the entire process becomes more efficient, transparent, and effective.
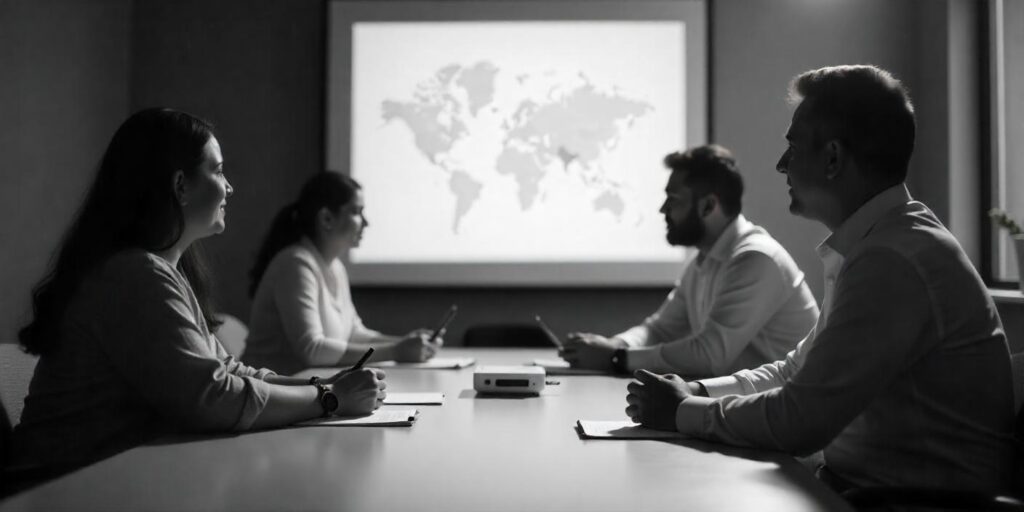
Case Study:
A pharmaceutical firm struggling with quality inconsistencies implemented a collaborative CQV approach. By bringing quality assurance, engineering, and operations together, they achieved a 20% reduction in process deviations within the first year.
Truth #6 – CQV Can Improve Regulatory Audits
One of the major benefits of CQV is its role in regulatory readiness. With documented, repeatable processes, you can demonstrate a high standard of compliance, easing the burden during regulatory inspections.
A robust validation process reassures regulators that every aspect of production meets or exceeds standards, reducing audit stress. Regulatory bodies, like the FDA, value transparency and thoroughness, and CQV is the tool that helps demonstrate both.
Why Adopting a Proactive Approach to CQV Can Save Time and Money
CQV isn’t just about fixing issues after they happen; it’s about adopting a proactive stance that catches potential problems before they escalate. By anticipating risks and implementing preventive measures, companies can avoid costly downtime and quality issues.
A proactive approach involves regular equipment assessments, predictive maintenance, and data-driven decision-making. This not only ensures that systems run optimally but also reduces the likelihood of surprise breakdowns or compliance issues that could disrupt production.
Data Point:
According to a study by the International Society for Pharmaceutical Engineering (ISPE), companies with proactive CQV programs experience up to 40% fewer unplanned shutdowns, saving both time and money.
How Incepbio can help you with your CQV needs
Navigating CQV can be challenging, especially in highly regulated industries. That’s where we at Incepbio come in. Our team has the experience and expertise to guide you through every phase of the procedure, from initial commissioning to ongoing validation, ensuring compliance with the latest standards. Whether it’s streamlining documentation, facilitating cross-functional collaboration, or optimizing validation intensity, Incepbio has you covered. Visit incepbio.com to learn more about our tailored solutions.
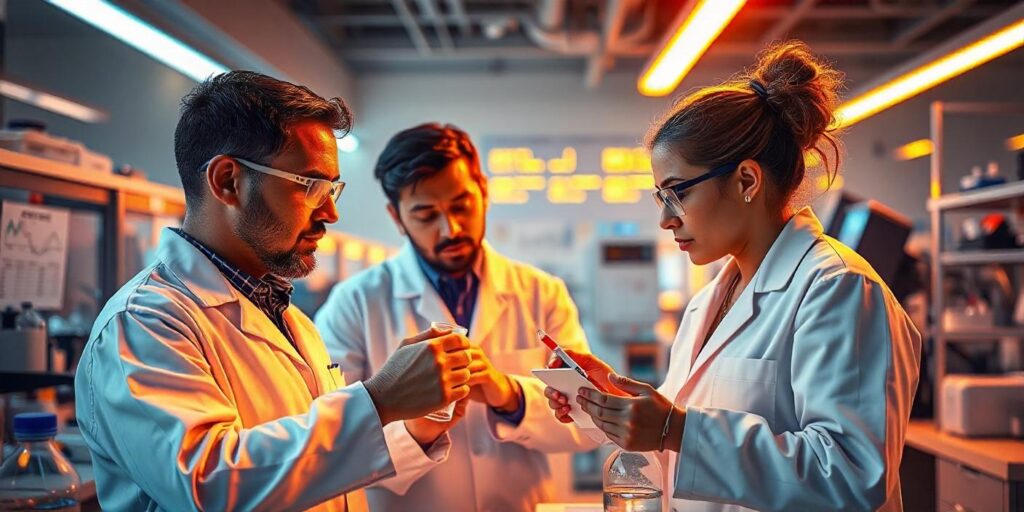
Conclusion
CQV isn’t just about checking off boxes. It’s an ongoing commitment to quality, efficiency, and compliance that can make or break your operations. By understanding these six truths about the validation process, you’re equipped to turn CQV from a regulatory burden into a strategic asset.
Remember, with the right CQV strategy, you’re not just meeting today’s standards—you’re setting your business up for long-term success. Ready to take the next step? Incepbio can help guide you on your journey.
Authors
-
Shubhankar is a pharmaceutical professional with over 10 + years of experience in Drug Substance (Upstream), Aseptic Batch Manufacturing (Drug Product), Process Validation, and CQV (Commissioning, Qualification, and Validation). He is skilled in managing the qualification and implementation of protocols for URS, DQ, FAT, SAT, IQ, OQ, and PQ for new equipment. Holds sounds knowledge of CSV (Computer System Validation) in compliance with 21 CFR 210/211, 21 CFR Part 11, and European regulations. Shubhankar is experienced in creating cGMP-oriented documentation, including SOPs, BPRs, Calibration Records, and deviation investigations. Expertise in overseeing various validation activities, such as HVAC, Utility, and Process Equipment Validation.
View all posts -
An experienced SEO professional, Adithya is someone fascinated by the art of content creation. He has published over 700 articles under his name. Additionally, he has worked for companies like TCS, Essentially Sports, and holds expertise in the field of digital marketing
View all posts -
Arjun Jha has over 8 years of experience in tech startups, business strategy, and digital and traditional marketing. He’s helped many startups grow by using creative strategies and a deep understanding of the market. Outside of work, Arjun enjoys reading about business, philosophy, psychology, and spirituality, which inspires his unique approach to problem-solving and growth.
View all posts