Temperature control is a critical element in industries where product integrity and safety depend on precise environmental conditions. Whether you’re involved in pharmaceutical manufacturing, medical device production, or food processing, the need for consistent temperature control is undeniable. Thermal validation is the process that guarantees your critical systems, equipment, and environments maintain the necessary temperatures for safe and effective product handling.
In this comprehensive guide, we will break down the importance of thermal validation, the process itself, common challenges you might face, and how Incepbio can help ensure your processes stay compliant and efficient. Whether you’re validating a storage room, a production line, or transportation systems, this blog will help you understand the principles behind thermal validation and how to apply them.
What is Thermal Validation?
Thermal validation is the systematic process of ensuring that temperature-controlled environments, systems, and equipment consistently maintain the required temperature within specified limits. This practice is critical in industries that handle temperature-sensitive products, such as pharmaceuticals, biotechnology, food processing, and medical device manufacturing, where even slight variations in temperature can compromise the quality, safety, and efficacy of products.
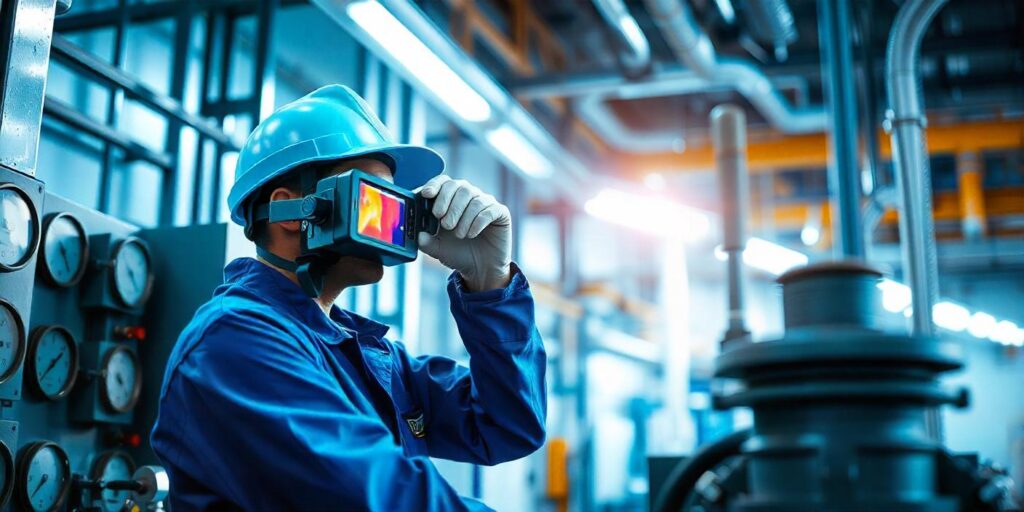
Temperature-sensitive products, such as vaccines, biologics, medications, and medical devices, need to be stored, transported, and processed within precise temperature ranges. Deviations from these conditions could lead to degradation, loss of potency, contamination, or non-compliance with regulatory standards. Therefore, thermal validation ensures that these products are handled in the right conditions, from manufacturing through to distribution.
Key Objectives of Thermal Validation
- Temperature Consistency:
The primary goal of thermal validation is to confirm that equipment or environments maintain a consistent temperature within the prescribed limits, whether it’s for refrigerators, freezers, cold chain transport, or manufacturing environments. - Regulatory Compliance:
Regulatory authorities like the FDA, EMA, WHO, and ISO mandate strict guidelines for temperature control, particularly for pharmaceutical and biotech products. Thermal validation is essential for ensuring compliance with these regulations, helping companies avoid penalties, recalls, and damage to brand reputation. - Product Integrity and Safety:
By validating temperature conditions, companies can be confident that their products remain safe, effective, and of high quality throughout their lifecycle. This is particularly crucial for life-saving therapies and vaccines, where even minor temperature fluctuations could result in compromised efficacy. - Process Optimization:
Thermal validation ensures that temperature-sensitive processes, such as sterilization, storage, transportation, or processing, are carried out within optimal conditions, minimizing the risk of product loss or contamination.
Steps in Thermal Validation
Thermal validation is a comprehensive process that involves several stages, each designed to test and ensure that temperature control systems meet the required standards.
1. Initial Planning and Risk Assessment
Before conducting thermal validation, a thorough risk assessment is performed to identify potential challenges and determine the critical temperature points for validation. During this stage:
- The temperature range for each product or environment is defined.
- Equipment, systems, or areas to be validated are identified.
- A validation plan is developed, detailing the methodology, testing protocols, and required documentation.
Read More: What Are Turnkey Projects? A Complete Guide for Beginners
2. Calibration of Equipment
Before testing, the equipment used for temperature monitoring, such as data loggers, sensors, or thermometers, must be calibrated against known standards to ensure accuracy. Calibration ensures that the data collected during validation is reliable and reflects the true temperature of the environment or system.
3. Mapping and Data Collection
Once the system or environment is calibrated, the next step is thermal mapping. During thermal mapping, temperature sensors are strategically placed in various locations to capture temperature variations across the area. This is particularly important for refrigerators, freezers, or cold storage warehouses, where temperature can vary from one spot to another.
- Data loggers record temperature at defined intervals over a specific period (e.g., 24-48 hours or more, depending on the validation requirements).
- Mapping helps identify hot spots, cold spots, or areas that may be prone to temperature fluctuations.
4. Stability Testing
After the initial mapping, stability testing is performed to ensure the environment or system can maintain the required temperature over time. The system is subjected to normal operating conditions, and temperature data is continuously collected to verify consistency. This step helps identify any long-term stability issues and confirms whether the system can maintain compliance over extended periods.
5. Documentation and Reporting
As a crucial component of thermal validation, documentation is key for compliance with regulatory standards. After testing, all data collected during the validation process must be compiled into a detailed validation report that includes:
- Temperature profiles and test results.
- Calibration certificates for equipment used.
- Mapping data and location of sensors.
- Deviation analysis if any temperature excursions occurred during testing.
The final report serves as proof that the system meets the required standards and regulatory expectations.
6. Ongoing Monitoring and Revalidation
Thermal validation is not a one-time process. Continuous monitoring is essential to ensure ongoing compliance. In addition to initial validation, systems should be regularly tested and recalibrated to confirm that temperature conditions are consistently maintained.
- Automated monitoring systems with real-time alerts can help identify temperature deviations immediately.
- Revalidation is conducted periodically or after changes to systems, equipment, or environmental conditions (e.g., installation of new cooling units, modifications to storage areas).
Read More: Thermal Validation: 8 Critical Regulatory Standards You Must Know
Why is Thermal Validation Crucial for Pharmaceutical Companies?
Thermal validation is essential for pharmaceutical companies due to the critical role temperature plays in ensuring the safety, efficacy, and quality of pharmaceutical products. Temperature-sensitive products such as vaccines, biologics, injectables, insulin, and cell-based therapies must be stored, transported, and processed within tightly controlled temperature ranges. Any deviation from these ranges can lead to the degradation of the product, resulting in compromised patient safety, loss of product integrity, and regulatory non-compliance.
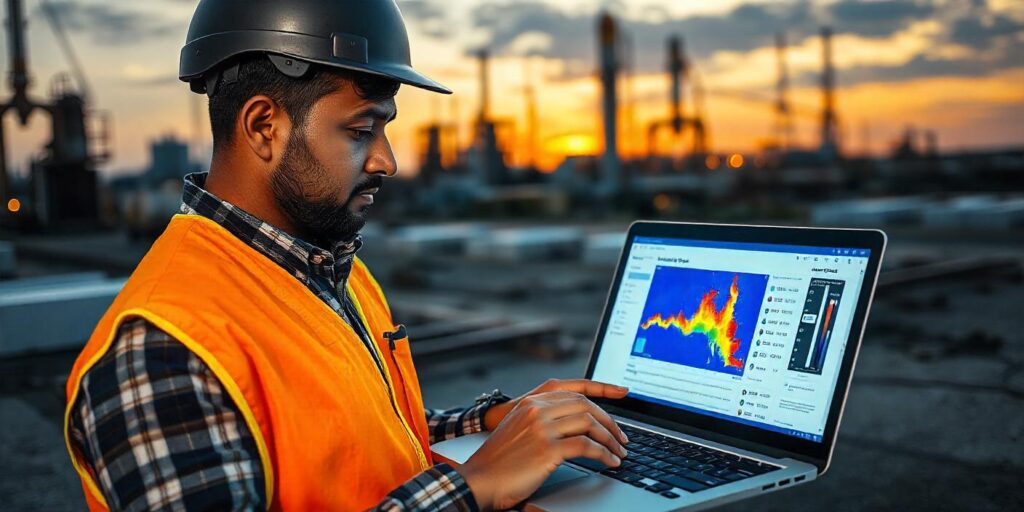
Here’s why thermal validation is particularly crucial for pharmaceutical companies:
1. Ensuring Product Efficacy and Safety
Many pharmaceutical products, especially biologics, vaccines, and medications, are highly sensitive to temperature changes. Exposure to higher or lower temperatures than recommended can cause:
- Chemical degradation: Active ingredients may break down, leading to a loss of efficacy.
- Microbial growth: Improper storage temperatures can encourage bacterial or fungal contamination, especially in injectable products.
- Physical changes: Protein-based products or vaccines can undergo denaturation, reducing their effectiveness or making them unsafe for use.
Thermal validation ensures that products are maintained within their required temperature ranges, safeguarding their efficacy, potency, and safety throughout their lifecycle—from production to distribution to the point of use.
2. Compliance with Regulatory Standards
Pharmaceutical companies operate under strict regulatory oversight from authorities such as the FDA, EMA, WHO, and ISO. These organizations have established GMP (Good Manufacturing Practice) guidelines that include stringent requirements for the storage and transport of temperature-sensitive products.
Thermal validation helps companies meet these regulatory requirements by providing:
- Objective proof that temperature conditions are consistently maintained within defined limits.
- Audit-ready documentation: A detailed validation report that demonstrates compliance with regulatory standards during inspections.
Failure to comply with these regulations can result in product recalls, fines, delayed product launches, and a loss of market authorization.
3. Protecting Product Integrity During Distribution
For many pharmaceutical products, maintaining the cold chain during transportation is critical. Cold chain logistics involve carefully controlling the temperature of products throughout transportation, whether by air, land, or sea. This ensures that products, especially vaccines or biologic therapies, do not lose their potency or become ineffective due to improper temperature control.
Thermal validation enables pharmaceutical companies to:
- Map temperature fluctuations during transportation, identifying potential risks such as hot spots or cold spots.
- Ensure that temperature-controlled packaging and transportation methods are effective and compliant with product requirements.
Without proper thermal validation, pharmaceutical companies risk delivering ineffective or unsafe products to patients, which can severely damage the company’s reputation and result in costly regulatory actions.
Read More: Top 10 Challenges in Thermal Validation and How to Overcome Them
4. Minimizing Risk of Product Loss
Thermal deviations, even brief ones, can result in product spoilage and significant financial loss. The cost of discarding a batch of vaccines or biologics due to improper storage far outweighs the cost of performing regular thermal validation. In addition, pharmaceutical companies must factor in the costs of retesting, replacing products, and recalling products from the market, all of which can severely impact profit margins.
Thermal validation allows companies to:
- Prevent costly product waste by ensuring products remain within safe temperature limits.
- Maintain inventory integrity by continuously monitoring the temperature of products in storage or transit.
5. Increasing Operational Efficiency and Reliability
Regular thermal validation helps pharmaceutical companies identify and address any weaknesses in their temperature control systems, whether in storage facilities, distribution networks, or transportation logistics. By identifying issues early, companies can:
- Optimize energy usage by identifying and fixing inefficient temperature control systems.
- Reduce downtime in production and distribution, ensuring the smooth operation of critical processes.
- Implement more efficient systems for temperature monitoring and data logging.
This helps improve overall operational efficiency, ensuring the pharmaceutical supply chain runs smoothly while maintaining product safety and compliance.
6. Building Trust with Stakeholders
Pharmaceutical companies are held to high standards by regulatory authorities, healthcare providers, and consumers. Maintaining product integrity is crucial to upholding the reputation of a company. Properly validating temperature-controlled systems builds trust with:
- Regulators, by demonstrating adherence to industry standards.
- Customers, by ensuring that products are delivered as intended without degradation or loss of quality.
- Healthcare professionals, by providing assurance that the medications and therapies they prescribe are safe and effective.
Thermal validation strengthens the credibility of pharmaceutical companies, reassuring stakeholders that their products meet the highest safety and quality standards.
7. Facilitating Continuous Monitoring and Revalidation
Thermal validation doesn’t end with an initial test. Ongoing monitoring and revalidation are necessary to ensure that temperature conditions remain consistent over time. Pharmaceutical companies must periodically check that:
- Temperature monitoring systems remain calibrated.
- Changes in storage or transportation conditions don’t affect product integrity.
- Updated temperature control equipment continues to meet regulatory requirements.
Regular revalidation and continuous monitoring help identify potential issues before they become risks, ensuring sustained compliance and product integrity.
When Should You Conduct Thermal Validation?
Thermal validation is an essential process in industries handling temperature-sensitive products, particularly in the pharmaceutical, biotech, and medical device sectors. The timing of thermal validation depends on various factors such as regulatory requirements, changes to processes, and the introduction of new equipment or systems. Below are the key instances when thermal validation should be conducted:
1. During New Facility Setup or Equipment Installation
Whenever a new facility, storage area, or equipment is set up, thermal validation should be one of the first steps. This includes:
- New cold storage rooms: Such as refrigerators, freezers, or controlled temperature environments.
- New temperature-sensitive equipment: Any new refrigeration systems, incubators, or cold chain transport systems.
- Upgraded or expanded facilities: When a pharmaceutical company adds new storage areas or modifies existing ones.
This ensures that the facility or equipment meets the required temperature control specifications and complies with industry regulations right from the start.
2. After Significant Changes to Equipment or Systems
Thermal validation is necessary anytime changes are made to the systems or equipment involved in temperature control, such as:
- Upgrades to HVAC systems (Heating, Ventilation, and Air Conditioning) or changes in airflow design.
- Installation of new temperature monitoring sensors or data loggers.
- System recalibration or replacement of critical temperature control equipment, like refrigerators or freezers.
Even small changes, like altering the layout of storage areas, can impact temperature consistency and warrant revalidation.
3. When New Temperature-Sensitive Products Are Introduced
Each temperature-sensitive product has specific storage temperature requirements. When a new product is introduced, thermal validation should be conducted to ensure:
- The new product’s specific temperature requirements are met during storage, transportation, and handling.
- The cold chain logistics (such as shipping and delivery systems) are equipped to handle the product without exceeding temperature limits.
For example, if a company starts storing a new biologic, vaccine, or temperature-sensitive medical device, validation will ensure the product’s integrity and compliance with regulatory guidelines.
4. In Response to Regulatory Requirements or Audits
Thermal validation should be conducted in response to regulatory inspections or audits to demonstrate compliance with the required standards. This may include:
- FDA inspections: Especially in industries like pharmaceuticals and biologics where temperature control is crucial for product safety.
- GxP (Good Practice) audits: In response to audits that require confirmation of temperature consistency and monitoring.
- ISO or EU GMP audits: These standards often require companies to prove they have validated and documented thermal conditions for temperature-sensitive products.
Regulatory bodies require thorough documentation and testing to ensure compliance with temperature management regulations.
Read More: Thermal Validation: 5 New Cutting-Edge Technologies
5. During or After Significant Changes in Facility Operations
Thermal validation may be necessary when significant operational changes occur in the facility or storage environments, such as:
- Seasonal changes that may affect temperature conditions, especially in environments where external temperatures vary greatly.
- Modifications to the operating conditions, such as increasing the load on cold storage equipment or altering the use of refrigeration units.
- Changes in staff or operating procedures that might affect how temperature-sensitive materials are handled or stored.
These changes can impact temperature control systems, so validating temperature conditions ensures ongoing compliance and safety.
6. When Implementing New Cold Chain Logistics
For products that need to be transported under specific temperature conditions, thermal validation should be conducted when:
- A new cold chain logistics provider is engaged.
- Modifications to the packaging or transportation system are made, such as changes in insulated shipping containers or the introduction of new temperature-controlled vehicles.
- The route or delivery method for temperature-sensitive products is changed.
Thermal validation helps ensure the integrity of products during transportation, preventing temperature deviations that could affect product quality.
7. Periodically as Part of Ongoing Quality Assurance
Thermal validation should not be a one-time process; it must be conducted periodically to ensure ongoing compliance and product integrity:
- Routine revalidation: Regular thermal validation should be scheduled (e.g., annually or biannually) to verify that equipment and systems continue to operate within required temperature ranges.
- Continuous monitoring: Implementing automated systems to monitor temperature in real-time, combined with periodic validation, helps identify issues quickly before they lead to larger problems.
8. After Major Equipment Failure or System Malfunction
If there’s a malfunction or failure in a critical piece of temperature control equipment, such as a refrigeration unit or temperature sensor, validation should be performed to ensure that the system can still maintain the required temperature levels. This is especially important if the failure occurred during the storage or transportation of temperature-sensitive products.
9. When Starting a New Production or Batch Process
For pharmaceutical manufacturers or biotech companies, whenever a new batch or production process is initiated that involves temperature-sensitive products, thermal validation is required to confirm that the equipment and environments involved maintain temperature integrity throughout the process. This is particularly true for processes like sterilization, freeze-drying, or bioreactor operation.
Acceptance Criteria for Thermal Validation
Acceptance criteria for thermal validation are the specific conditions that must be met to confirm that the thermal environment (such as storage or transport conditions) consistently maintains the required temperature range for temperature-sensitive products. These criteria are established based on regulatory requirements, product specifications, and industry best practices.
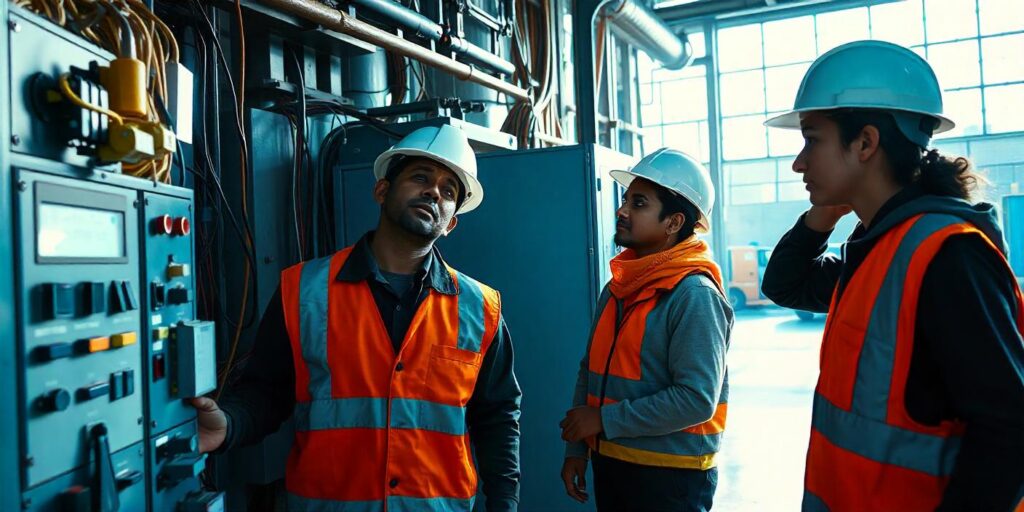
Here are the key components and standards used to define acceptance criteria for thermal validation:
1. Temperature Range Compliance
The most critical acceptance criterion for thermal validation is whether the temperature of the environment or system remains within the required range for the product. For pharmaceutical and biotechnology products, this is typically defined in terms of:
- Minimum and Maximum Temperatures: The temperature must not fall below the minimum or exceed the maximum specified limit.
- Product-Specific Temperature Requirements: Each product (e.g., vaccines, biologics, medical devices) will have specific temperature ranges defined by the manufacturer, such as:
- Refrigerated products (typically 2°C to 8°C)
- Frozen products (typically -20°C to -70°C)
- Room-temperature products (typically 15°C to 25°C)
The acceptance criteria typically specify that temperatures must stay within this range for a specified period, often with a defined tolerance level (e.g., ±2°C).
2. Time and Duration of Exposure
While temperature range compliance is crucial, the duration of exposure is equally important. Acceptance criteria typically include:
- Exposure Time Limits: The time the temperature-sensitive product is allowed to deviate from the specified range. For example, if the temperature goes out of range, the product may only be allowed to remain outside the limit for a specific duration (e.g., not more than 30 minutes at a temperature of 10°C for a product that should be stored at 4°C).
- Time in Transit: For cold chain logistics, the product may need to stay within the prescribed temperature range during transportation, including any transit delays.
Deviations outside of these limits must be investigated to assess the potential impact on product quality and safety.
3. Temperature Mapping and Uniformity
Temperature uniformity within a given space is essential to ensuring that all areas of the storage or transport environment meet the specified conditions. Acceptance criteria will include:
- Temperature Mapping: The process of measuring temperatures at various points within the storage area or transport unit. Acceptance criteria will define the acceptable temperature variations between different areas.
- Hot Spots and Cold Spots: The temperature variation between the hottest and coldest areas within the environment should not exceed a certain threshold. For example, temperature variations should not exceed ±2°C within a refrigerated unit.
- Airflow Considerations: Ensuring that the air circulation in a storage area or transport unit is adequate to maintain consistent temperature conditions, especially in large or complex environments.
4. Calibration of Temperature Monitoring Equipment
All temperature monitoring and recording devices must be properly calibrated before conducting thermal validation. Acceptance criteria related to equipment calibration include:
- Calibration Frequency: Temperature sensors, data loggers, and other monitoring devices should be calibrated at regular intervals, as defined by the manufacturer or regulatory standards.
- Accuracy and Precision: Monitoring equipment must meet specific accuracy requirements, often within ±0.5°C or better for sensitive products. Any discrepancies between the calibration standard and actual readings must be corrected before proceeding with validation.
5. System Recovery Time
In case of a temperature deviation (such as a power failure or equipment malfunction), the system must be able to return to the acceptable temperature range within a reasonable time frame. Acceptance criteria will often include:
- Recovery Time: The time it takes for the system to recover from an out-of-range condition and return to the specified temperature. For example, a refrigerator should return to the required temperature range within 30 minutes after being exposed to a deviation.
6. Documentation and Data Integrity
Regulatory bodies require comprehensive documentation to confirm that thermal validation criteria have been met. The acceptance criteria for documentation typically include:
- Complete and Accurate Data: All temperature data must be logged with accurate timestamps and location markers (for temperature mapping). Data logs must be stored securely and be readily available for audits.
- Traceability and Review: All validation activities should be traceable, and the raw data should be reviewed by qualified personnel to ensure compliance with the set criteria.
- Validation Report: A final report summarizing the validation process, results, deviations, and corrective actions should be produced.
7. Out-of-Tolerance Conditions
When deviations from the specified temperature range occur, acceptance criteria should define the acceptable threshold for corrective actions:
- Threshold for Deviation: Typically, any deviation beyond a set tolerance (e.g., ±2°C for refrigerated products) requires immediate action. The severity of the deviation and its duration must be evaluated to determine if the product is still viable.
- Investigation and Corrective Actions: When deviations occur, the cause of the deviation must be identified and addressed. Depending on the product and regulatory guidelines, the affected products may need to be quarantined, tested for stability, or discarded.
- Impact Assessment: Any deviation from the temperature range that exceeds the tolerance must be evaluated for its impact on the product’s integrity. This assessment should be documented and can require additional testing or analysis.
8. Compliance with Regulatory Standards
The final acceptance criterion involves ensuring that all thermal validation activities align with regulatory standards, which can include:
- FDA Guidelines: Compliance with FDA regulations related to temperature-sensitive pharmaceutical products.
- EU GMP: Adherence to European Good Manufacturing Practice guidelines for temperature control.
- ISO 9001 or ISO 14644: For companies seeking certification, validation must meet the relevant ISO standards for quality management systems and cleanroom environments.
All thermal validation processes should be conducted in compliance with these regulatory guidelines and include the necessary reporting and documentation to demonstrate compliance
Common Challenges in Thermal Validation and How to Overcome Them
Thermal validation is not without its challenges. Here are a few common obstacles and how to overcome them:
- Equipment Malfunctions: Instruments such as temperature sensors can fail, leading to inaccurate readings. To mitigate this risk, it’s important to calibrate equipment regularly and have backup systems in place.
- Temperature Fluctuations: Environmental factors or operational errors can cause temperature fluctuations. A comprehensive monitoring system will help you identify and correct these fluctuations quickly.
- Human Error: Manual oversight or poor training can lead to mistakes. Ensuring staff are properly trained and that clear procedures are in place can minimize this risk.
Read More: 8 Secrets You Must Know for Best Thermal Validation Results
Key Tools and Techniques for Successful Thermal Validation
Successful thermal validation requires the use of specialized tools and techniques. Let’s explore some of them:
Temperature Mapping
Temperature mapping is the process of measuring and documenting temperature variations across different areas of a facility. This technique helps identify cold or hot spots within a cleanroom, storage unit, or transportation container.
Use of Data Loggers and Sensors
Temperature data loggers and sensors are essential for capturing accurate temperature data. These tools record temperature readings over time, allowing for detailed analysis of any deviations.
Real-time Monitoring Systems
For continuous validation, real-time temperature monitoring systems are invaluable. These systems track temperature conditions 24/7, alerting you to any fluctuations before they become a problem.
How Incepbio Can Simplify Thermal Validation
Incepbio offers comprehensive thermal validation services for pharmaceutical and medical device companies. Our team of experts will work with you to design, execute, and document a tailored thermal validation plan that ensures compliance and product integrity. Visit incepbio.com to learn how we can assist with your thermal validation needs.
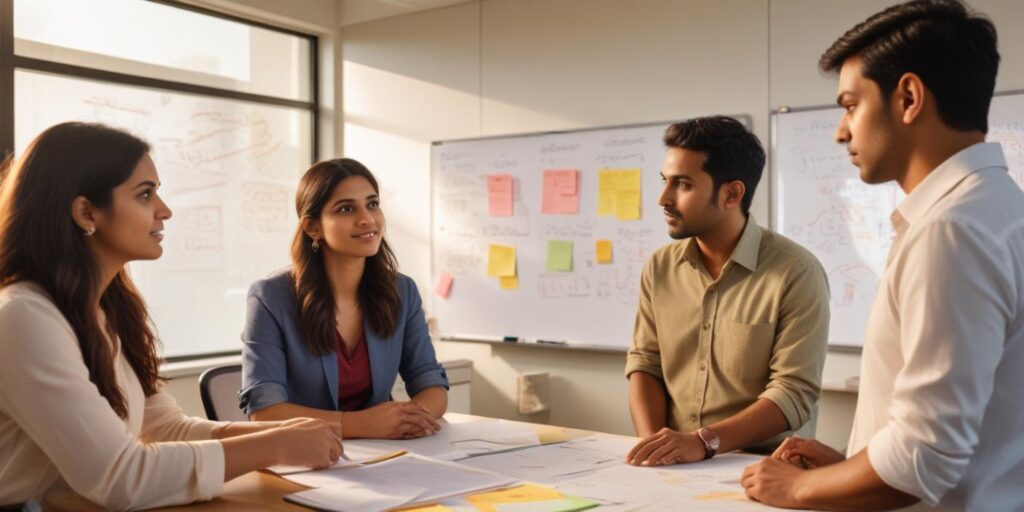
FAQs About Thermal Validation
- What is thermal validation?
Thermal validation ensures that temperature-sensitive processes or products are maintained within specified temperature ranges. - How do you perform thermal validation?
Thermal validation involves identifying critical temperature points, designing a protocol, conducting validation studies, analyzing results, and documenting findings. - Why is thermal validation important in pharmaceuticals?
Proper thermal validation ensures product integrity, regulatory compliance, and safety in the pharmaceutical industry. - How often should thermal validation be conducted?
Thermal validation should be conducted whenever there are changes to the process, equipment, or environmental conditions, and at regular intervals as required by regulations. - What tools are used in thermal validation?
Common tools include temperature sensors, data loggers, and real-time monitoring systems. - Can thermal validation be automated?
Yes, thermal validation can be automated using data logging and real-time monitoring systems. - What are the challenges of thermal validation?
Challenges include equipment failure, temperature fluctuations, and human error. - How can thermal validation improve product quality?
By ensuring temperature consistency, thermal validation prevents degradation and preserves the efficacy of temperature-sensitive products. - What are the compliance requirements for thermal validation?
Compliance requirements vary by industry but typically include adherence to FDA, EMA, and ISO standards. - How can Incepbio assist with thermal validation?
Incepbio offers expert thermal validation services, ensuring your systems are compliant and optimized for temperature-sensitive products.
Conclusion
Thermal validation is an essential process in industries that require precise temperature control for product safety and regulatory compliance. By following best practices, using the right tools, and working with experts like Incepbio, you can ensure that your systems remain efficient and compliant. If you’re ready to implement thermal validation in your processes, contact Incepbio today to get started.
Authors
-
-
Arjun Jha has over 8 years of experience in tech startups, business strategy, and digital and traditional marketing. He’s helped many startups grow by using creative strategies and a deep understanding of the market. Outside of work, Arjun enjoys reading about business, philosophy, psychology, and spirituality, which inspires his unique approach to problem-solving and growth.
View all posts -
An experienced SEO professional, Adithya is someone fascinated by the art of content creation. He has published over 700 articles under his name. Additionally, he has worked for companies like TCS, Essentially Sports, and holds expertise in the field of digital marketing
View all posts