When it comes to pharmaceutical and medical device manufacturing, there’s no room for error. One crucial process that ensures product safety and regulatory compliance is CQV—Commissioning, Qualification, and Validation. This three-step approach is the backbone of ensuring that your equipment, systems, and processes function as intended and meet stringent industry standards.
But here’s the thing: while the process is designed to catch risks and ensure compliance, there are hidden dangers that can undermine even the best-laid plans. These challenges often creep in unnoticed, jeopardizing timelines, budgets, and, most importantly, product quality and patient safety. Understanding these risks is key to avoiding costly mistakes and maintaining a competitive edge in a heavily regulated industry.
This blog will explore the hidden pitfalls of CQV, why they occur, and how you can mitigate them effectively. Whether you’re a seasoned professional or new to the process, this guide is packed with actionable insights to help you navigate the process with confidence.
What is CQV, and Why is it Crucial in Pharma and Medical Devices?
CQV stands for Commissioning, Qualification, and Validation—three interconnected steps that ensure your systems, equipment, and processes are ready for safe and compliant production. Think of CQV as your safety net to catch potential risks before they become costly mistakes.
Did you know that CQV (Commissioning, Qualification, and Validation) is crucial for ensuring compliance with global regulatory standards set by major authorities like the FDA, EMA, and WHO? This process is more than just a set of procedures—it forms the backbone of pharmaceutical, biotechnology, and medical device manufacturing to ensure that every product is safe, effective, and compliant with international regulations.
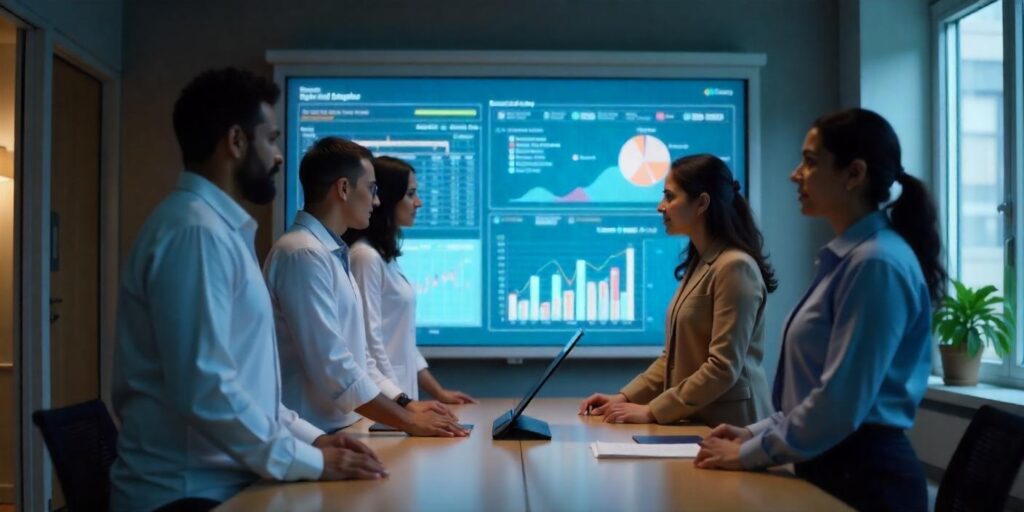
Without a robust CQV process, companies face significant risks, including non-compliance with regulatory standards, costly product recalls, legal liabilities, and potential damage to their reputation. Regulatory bodies require manufacturers to provide documented proof that their systems and processes are validated, operational, and consistently perform as intended. CQV ensures that these systems meet not only regulatory expectations but also industry best practices, ultimately safeguarding patient safety.
What Are the Hidden Dangers of Performing CQV?
1. Inadequate Pre-Planning
The Danger: Skipping the planning phase can lead to a lack of clarity in roles, responsibilities, and timelines. This disorganization often results in missed steps, rework, delays, and even non-compliance.
Without a well-defined CQV strategy, critical elements like risk assessments, resource allocation, and proper scheduling can be overlooked. This can cause confusion about deliverables, affecting timelines and quality. Pre-planning should involve thorough risk management, identifying key milestones, and ensuring that all involved parties have a clear understanding of the project’s scope.
Read More: 7 Tips to Train Your Team Better on Compliance
Action Tip: Develop a detailed plan that outlines the objectives, timelines, responsibilities, and methodologies. Engage key stakeholders early to ensure alignment and clarity.
2. Overlooking Vendor Qualifications
The Danger: Assuming that a vendor meets regulatory requirements without verifying their credentials can lead to equipment or materials that fail during qualification or do not meet the necessary standards.
Vendors play a critical role in the CQV process, and overlooking their qualifications can have serious consequences. A vendor’s lack of compliance with Good Manufacturing Practices (GMP) or regulatory standards can introduce risks into the system that compromise the final product’s quality or safety. Vendors may also fail to provide the proper documentation, certifications, or post-delivery support, creating compliance challenges.
Action Tip: Always vet vendors thoroughly, ensuring they are qualified and have a proven track record in meeting industry standards. Ask for references, conduct audits, and check certifications to ensure they align with your CQV goals.
3. Insufficient Documentation Practices
The Danger: Poor documentation can create gaps in traceability, which is crucial for compliance and auditing purposes. Inadequate records can result in missed inspections, delays, or even failure during audits.
Documentation is the backbone of CQV. Every stage of the process needs clear, precise, and easily retrievable records. Without proper documentation, it becomes difficult to prove that each step of the process met the required standards. Inadequate record-keeping can also complicate troubleshooting, as the root causes of any issues cannot be easily traced back to their origin.
Action Tip: Adopt a rigorous documentation management system that captures each phase of CQV. Ensure that all records are detailed, accurate, and stored securely in an easily accessible format for internal and external audits. Invest in electronic systems to reduce human error.
4. Ignoring Cross-Functional Collaboration
The Danger: Relying on one department to handle all aspects of CQV without collaboration can lead to siloed operations, miscommunication, and delays in project execution.
CQV is inherently a multidisciplinary process. Departments such as QA, engineering, operations, and regulatory need to be closely involved throughout to ensure compliance and operational efficiency. A lack of cross-functional collaboration can lead to misunderstandings, missed requirements, and implementation failures. Moreover, different teams might interpret the requirements differently, resulting in inefficiencies or non-compliance issues.
Action Tip: Foster open communication between all teams involved in CQV. Regular cross-functional meetings, progress updates, and clear channels for feedback can help ensure alignment and smooth execution of tasks. Early involvement from all departments ensures everyone is on the same page and that all aspects of the system are tested and validated.
Read More: 9 Emerging Technologies in the CQV Process
5. Neglecting Change Control Processes
The Danger: Failing to assess and manage changes during the CQV process can introduce unknown risks, leading to deviations in product quality or system functionality.
The CQV process must adapt to changes, but every change—whether it’s a design alteration, process modification, or addition—needs to be properly assessed for its impact on the system. A failure to implement proper change control protocols can lead to unforeseen problems, such as equipment malfunctions, missed regulatory requirements, or compromised product quality. Additionally, poorly documented changes can complicate validation efforts, especially if changes are made without revisiting earlier stages of testing.
Action Tip: Establish a robust change control process that evaluates the potential impact of all changes. Implement a structured review and approval process for any adjustments to the CQV plan or execution. This will help ensure that modifications do not undermine the quality or compliance of the system.
How Can You Avoid These Pitfalls?
Developing a Comprehensive CQV Strategy
Plan ahead! Use tools and templates to create a structured CQV process. Identify potential risks and outline mitigation strategies before starting.
Choosing the Right Vendors
Pick vendors who meet your quality and compliance standards. Regularly monitor their performance to ensure they’re delivering what’s promised.
Read More: 6 Things to Know When You Are Choosing Your CQV Compliance Partner
Emphasizing Robust Documentation
Use checklists and templates to maintain consistency in documentation. Detailed records make audits easier and ensure compliance.
Encouraging Cross-Functional Engagement
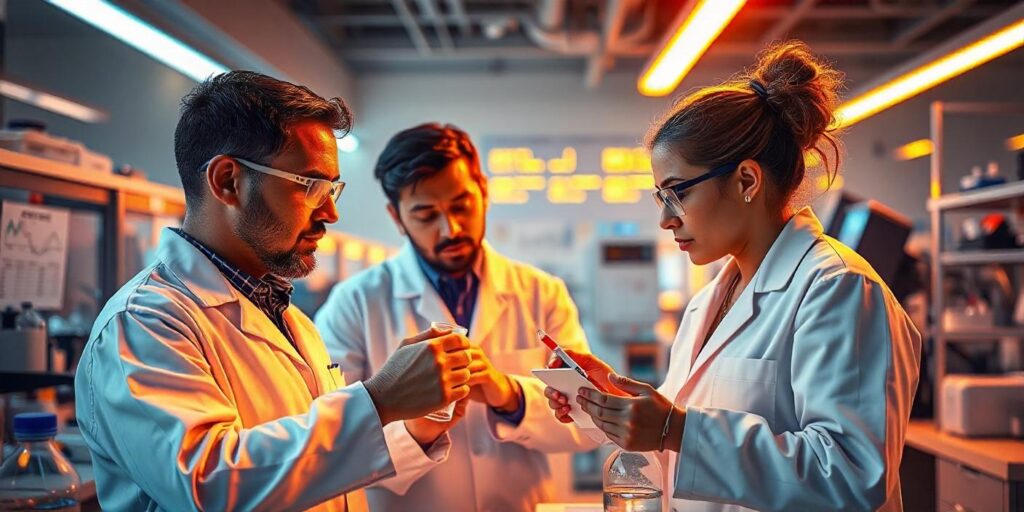
Bring all stakeholders to the table early. Regular meetings and open communication can prevent missteps and promote efficiency.
Strengthening Change Control Protocols
Train your team to handle unexpected changes effectively. Use change control software to track and evaluate the impact of modifications.
Why Staying Vigilant During CQV is Non-Negotiable
Real-world examples show that CQV failures can lead to product recalls, financial losses, and damaged reputations. Staying proactive and addressing potential risks upfront can save your company from costly mistakes.
Final Thoughts on Mitigating CQV Risks
CQV is your key to maintaining compliance and producing safe, high-quality products. By avoiding hidden dangers and approaching CQV strategically, you can protect your operations and your customers.
Ready to optimize your CQV process? Contact Incepbio today for expert guidance! Click here to learn more about our services.
Authors
-
Shubhankar is a pharmaceutical professional with over 10 + years of experience in Drug Substance (Upstream), Aseptic Batch Manufacturing (Drug Product), Process Validation, and CQV (Commissioning, Qualification, and Validation). He is skilled in managing the qualification and implementation of protocols for URS, DQ, FAT, SAT, IQ, OQ, and PQ for new equipment. Holds sounds knowledge of CSV (Computer System Validation) in compliance with 21 CFR 210/211, 21 CFR Part 11, and European regulations. Shubhankar is experienced in creating cGMP-oriented documentation, including SOPs, BPRs, Calibration Records, and deviation investigations. Expertise in overseeing various validation activities, such as HVAC, Utility, and Process Equipment Validation.
View all posts -
An experienced SEO professional, Adithya is someone fascinated by the art of content creation. He has published over 700 articles under his name. Additionally, he has worked for companies like TCS, Essentially Sports, and holds expertise in the field of digital marketing
View all posts -
Arjun Jha has over 8 years of experience in tech startups, business strategy, and digital and traditional marketing. He’s helped many startups grow by using creative strategies and a deep understanding of the market. Outside of work, Arjun enjoys reading about business, philosophy, psychology, and spirituality, which inspires his unique approach to problem-solving and growth.
View all posts